Зубчатые передачи служат для. Общие сведения и классификация зубчатых передач. Виды передачи движения
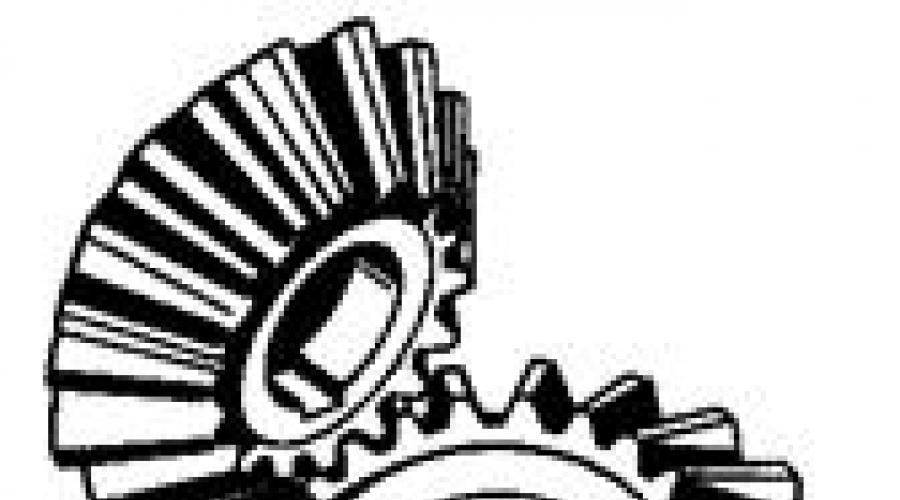
Читайте также
Описание зубчатых передач
ОБЩИЕ СВЕДЕНИЯ О ЗУБЧАТЫХ ПЕРЕДАЧАХ
Зубчатые передачи являются разновидностью механических передач, работающих на принципе зацепления. Их используют для передачи и преобразования вращательного движения между валами.
Зубчатые передачи отличаются высоким КПД (для одной ступени – 0,97-0,99 и выше), надежностью и длительным сроком службы, компактностью, стабильностью передаточного отношения из-за отсутствия проскальзывания. Зубчатые передачи применяют в широком диапазоне скоростей (до 200 м/сек), мощностей (до 300 МВт). Размеры зубчатых колес могут быть от долей миллиметра до нескольких метров.
К недостаткам можно отнести сравнительно высокую сложность изготовления, необходимость нарезания зубьев с высокой точностью, шум и вибрация при высоких скоростях, большую жесткость, не позволяющая компенсировать динамические нагрузки.
Передаточные числа в редукторных передачах могут достигать 8, в открытых передачах – до 20, в коробках передач – до 4.
По расположению зубьев различают передачи с наружным и внутренним зацеплением.
Конструктивно зубчатые передачи большей частью выполняются закрытыми в общем жестком корпусе, что обеспечивает высокую точность сборки. Лишь тихоходные передачи (v < 3 м/сек) с колесами значительных размеров, нередко встроенных в конструкцию машин (например, в механизмах поворота подъемных кранов, станков), изготавливаются в открытом исполнении.
Чаще всего зубчатые передачи применяют в качестве замедлительных (редукторов), т.е. для уменьшения частоты вращения и увеличения вращающего момента, но также с успехом используются для повышения скорости вращения (мультипликаторы).
Для предохранения рабочих поверхностей зубьев от заедания и абразивного износа, а также для уменьшения потерь на трение и связанного с этим нагревания, применяют смазку. Закрытые передачи обычно смазываются жидкими минеральными маслами, окунанием колес или принудительной подачей масла к зацепляющимся зубьям. Открытые передачи смазываются консистентными смазками, периодически наносимыми на зубья.
Зубчатые передачи с параллельными валами называются цилиндрические (рис. 2.1), с пересекающимися валами – конические (рис. 2.2).
По расположению зубьев различают передачи с наружным (рис. 2.1а -в ) и внутренним зацеплением (рис. 2.1г ).
По профилю зубьев колес передачи подразделяют: на передачи с эвольвентным зацеплением , в котором профили зубьев очерчены эвольвентами; на передачи с циклоидальным профилем ; на передачи с зацеплением Новикова . Далее в пособии будут описываться только передачи эвольвентного профиля с наружным зацеплением.
Шестерня – это зубчатое колесо передачи с меньшим числом зубьев (чаще всего – ведущее). Колесо – это зубчатое колесо передачи с большим числом зубьев. Термин "зубчатое колесо" можно применять как к шестерне, так и к колесу зубчатой передачи.
Цилиндрические зубчатые передачи бывают прямозубыми, косозубыми и шевронными.
Прямозубые колеса (рис. 2.1а ) применяют преимущественно при невысоких и средних окружных скоростях, при большой твердости зубьев (когда динамические нагрузки от неточностей изготовления невелики по сравнению с полезными), в планетарных передачах, в открытых передачах, а также при необходимости осевого перемещения колес (в коробках передач).
Косозубые колеса (рис. 2.1б ) обладают более высокой нагрузочной способностью (за счет большей длины зуба при одинаковой ширине зубчатого венца), повышенной плавностью и пониженной шумностью, поэтому их применяют для ответственных передач при средних и высоких скоростях. Объем их применения – свыше 40 % объема применения всех цилиндрических колес в машинах.
Косозубые колеса с твердыми поверхностями зубьев требуют повышенной защиты от загрязнений во избежание неравномерности износа по длине контактных линий и опасности выкрашивания. В косозубом зацеплении возникает осевая сила, которую надо учитывать при проектировании опор и валов.
Шевронные колеса (рис. 2.1в ) обладают всеми преимуществами косозубых колес, и при этом отсутствует вредная осевая сила, но их технология изготовления сложней.
Для прямозубых колес угол наклона зубьев b = 0°, для косозубых - b = 8...20°, для шевронных - b = 25...40°.
В косозубых передачах редукторов для шестерен рекомендуют принимать направление зуба левое, для колес – правое.
Большинство серийных редукторов имеют косозубые колеса, причем и в быстроходных и в тихоходных ступенях.
Среди конических зубчатых передач наибольшее распространение в машиностроении имеют передачи с прямыми зубьями. Также часто применяются передачи с круговыми зубьями. Гораздо реже – с тангенциальными и другими криволинейными зубьями.
![]() | ![]() | ||
а | б | ||
Рис. 2.2. Виды конических зубчатых передач |
Прямозубые конические передачи (рис. 2.2а ) применяют при невысоких окружных скоростях (до 2…3 м/сек, допустимо до 8 м/сек), как наиболее простые в монтаже.
Конические передачи с круговыми зубьями (рис. 2.2б ) имеют более плавное зацепление и поэтому большие быстроходность и несущую способность. Они более технологичны.
2.3Материалы зубчатых колес и термическая или химико-термическая обработка
Материалы зубчатых колес и термическая или химико-термическая обработка выбираются в зависимости от назначения передачи, условий эксплуатации и требований к габаритным размерам.
Для повышения несущей способности передач целесообразно повышение твердости поверхности зубьев, т.к. несущая способность передач по контактной прочности пропорциональна квадрату твердости поверхности зубьев. Однако повышение твердости материала отрицательно сказывается на изгибной прочности. Для повышения изгибной прочности желательно сохранять вязкую сердцевину зуба. Поэтому в основном применяется поверхностная термическая или химико-термическая обработка.
Способы упрочнения :
· Нормализация позволяет получить твердость 180…220 HB, поэтому нагрузочная способность относительно невелика, но при этом зубья колес хорошо прирабатываются и сохраняют точность, полученную при механической обработке. Нормализованные колеса обычно используют во вспомогательных механизмах, например, в механизмах ручного управления.
Применяемые стали: 40, 45, 50 и др. Для повышения стойкости против заедания шестерни и колеса следует изготавливать из разных материалов.
· Улучшение позволяет получить твердость поверхности и сердцевины 200…240 HB (для небольших шестерен 280…320 HB), нагрузочная способность несколько выше, чем при нормализации, но зубья колес прирабатываются хуже. Обычно улучшенные колеса применяют в условиях мелкосерийного и единичного производства при отсутствии жестких требований к габаритам.
Применяемые стали: 40, 45, 50Г, 35ХГС, 40Х и др.
· Закалка токами высокой частоты (ТВЧ) дает среднюю нагрузочную способность при достаточно простой технологии упрочнения. Позволяет достигать поверхностной твердости 45…55 HRC при глубине упрочненного слоя до 3…4 мм. Закалке ТВЧ обычно предшествует улучшение, поэтому механические свойства сердцевины – как при улучшении. Изгибная прочность по сравнению с объемной закалкой выше в 1,5-2 раза. Из-за повышенной твердости зубьев передачи плохо прирабатываются. Размеры зубчатых колес практически неограниченны. Необходимо помнить, что при модулях менее 3…5 мм, зуб прокаливается насквозь, что приводит к значительному их короблению и снижению ударной вязкости.
Применяемые стали: 40Х, 40ХН, 35ХМ, 35ХГСА.
· Цементация (поверхностное насыщение углеродом) с последующей закалкой ТВЧ и обязательной шлифовкой позволяет получить поверхностную твердость 56…63 HRC при глубине упрочненного слоя 0,5…2 мм. Нагрузочная способность высокая, но технология упрочнения более сложная. Изгибная прочность по сравнению с объемной закалкой выше в 2-2,5 раза.
Широко применяют сталь 20Х, а для ответственных зубчатых колес, особенно работающих с перегрузками и ударными нагрузками, стали 12ХН3А, 20ХНМ, 18ХГТ, 25ХГМ, 15ХФ.
· Азотирование (поверхностное насыщение азотом) обеспечивает высокую твердость и износостойкость поверхностных слоев, при этом не требуется последующая закалка и шлифование. Азотирование позволяет получить поверхностную твердость 58…67 HRC при глубине упрочненного слоя 0,2…0,5 мм. Малая толщина упрочненного слоя не позволяет применять азотированные колеса при ударных нагрузках и при работе с интенсивным изнашиванием (при загрязненной смазке, попадании абразива). Длительность процесса азотирования достигает 40-60 часов. Обычно азотирование применяют для колес с внутренним зацеплением и других, шлифование которых затруднено.
Применяют молибденовую сталь 38Х2МЮА, но возможно азотирование сталей 40ХФА, 40ХНА, 40Х до меньшей твердости, но большей вязкости.
· Нитроцементация – насыщение поверхностных слоев углеродом и азотом в газовой среде с последующей закалкой обеспечивает высокую контактную прочность, износостойкость и сопротивление заеданиям, обладает достаточно высокой скоростью протекания процесса – около 0,1 мм/час и выше. В связи с малым короблением позволяет во многих случаях обойтись без шлифования. Содержание азота в поверхностном слое позволяет применять менее легированные стали, чем при цементации: 18ХГТ, 25ХГТ, 40Х и др.
2.4Конструкция зубчатых колес
Конструкция зубчатых колес зависит от их размеров, материала, технологии изготовления и эксплуатационных требований.
Шестерни малых размеров, у которых диаметр окружности впадин зубьев близок к диаметру вала, выполняются за одно целое с валом (вал-шестерня) (рис. 2.3).
Колеса, допускающие посадку на вал, как правило, делаются насадными. Это дает возможность подбирать различные, наиболее подходящие материалы и термообработку для вала и колеса, упрощают технологию изготовления этих деталей, и позволяет после износа зубьев колеса производить его замену, сохраняя вал.
Шестерни небольшого диаметра (D £ 200 мм) обычно изготовляются из круглого проката (£ 150 мм), кованных или штампованных заготовок в виде сплошного диска или с выступающей ступицей и др. (рис. 2.4).
Колеса средних размеров (D £ 600 мм) изготовляются из поковок, штампованных или литых заготовок и большей частью имеют дисковую конструкцию (рис. 2.5).
Зубчатые колеса больших размеров можно изготовлять цельнолитыми, с одним или двумя параллельными дисками, подкрепленными ребрами, или со спицами крестовидного, таврового, двутаврового, овального или другой формы сечения (рис. 2.6).
При использовании высококачественных сталей для изготовления зубчатого венца, в целях экономии, колеса могут выполняться бандажированными (посадка с гарантированным натягом) или сборными (на призонных болтах, с помощью сварки или клея) (рис. 2.7).
1 Основные понятия о зубчатых передачах
1.1 Общие сведения
В зубчатой передаче движение передается с помощью зацепления пары зубчатых колес (рис. 1, а - в). Меньшее зубчатое колесо принято называть шестерней , большее - колесо м . Термин «зубчатое колесо» относится как к шестерне, так и к колесу. Параметрам шестерни приписывают индекс 1, параметрам колеса - индекс 2. Зубчатые передачи - самый распространенный вид механических передач, так как могут надежно передавать мощности от долей до десятков тысяч киловатт при окружных скоростях до 275 м/с.
Рис. 1. Цилиндрические зубчатые передачи внешнего зацепления
Зубчатые передачи широко применяют во всех отраслях машиностроения и приборостроения.
Достоинства. 1. Высокая надежность работы в широком диапазоне нагрузок и скоростей. 2. Малые габариты. 3. Большая долговечность. 4. Высокий к.п.д. 5. Сравнительно малые нагрузки на валы и подшипники. 6. Постоянство передаточного числа. 7. Простота обслуживания.
Недостатки. 1. Относительно высокие требования к точности изготовления и монтажа. 2. Шум при больших скоростях.
Классификация. В зависимости от взаимного расположения геометрических осей валов зубчатые передачи бывают: ц и л и н дрические- при параллельных осях (рис. 1); к о н и ч е с к и е - при пересекающихся осях (рис. 2, а, б); в и н т о вые - при скрещивающихся осях (рис. 3). Винтовые зубчатые передачи характеризуются повышенным скольжением в зацеплении и низкой нагрузочной способностью, поэтому имеют ограниченное применение.
Рис. 2. Конические зубчатые передачи: а - прямозубая; Рис. 3. Винтовая зубчатая
б- с круговым зубом; передача
Для преобразования вращательного движения в поступательное и наоборот применяют реечную передачу (рис. 4), которая является частным случаем цилиндрической зубча той передачи. Рейку рассматривают как колесо, диаметр которого увеличен до бесконечности.
Рис. 4. Реечная передача Рис. 5. Цилиндриче ская прямозубая пере дача внутреннего Ы. за цеплении
В зависимости от расположения зубьев на ободе колес различают (см. рис. 1) передачи: прямозубые (а), к о с о з у б ы е (б), ш е в р о н н ы е (в) и с круговыми зубьями (см. рис. 2, б).
В зависимости от формы профиля зуба передачи бывают: эвольвентные, с зацеплением Новикова, циклоидальные. В современном машиностроении широко применяют эвольвентное зацепление .
В 1954 г. М. Л. Новиков предложил принципиально новое зацепление, в котором профиль зуба очерчен дугами окружностей. Это зацепление возможно лишь при косых зубьях.
Циклоидальное зацепление в настоящее время сохранилось в приборах и часах.
В зависимости от взаимного расположения колес зубчатые передачи бывают в н е ш н е г о (см. рис. 1) и в н у т р е н н е г о (рис. 5) зацепления. Ниже рассматриваются передачи внешнего зацепления, как наиболее распространенные.
В зависимости от конструктивного исполнения различают о т к р ы т ы е и з а к р ы т ы е зубчатые передачи. В открытых передачах зубья колес работают всухую или периодически смазываются пластичным смазочным материалом и не защищены от влияния внешней среды. Закрытые передачи помещаются в пыле- и влагонепроницаемые корпуса (картеры) и работают в масляной ванне (зубчатое колесо погружают в масло на глубину до ⅓ радиуса).
В зависимости от числа ступеней зубчатые передачи бывают о д н о- и м н о г о с т у п е н ч а т ы е.
В зависимости от относительного характера движения валов различают р я д о в ы е зубчатые передачи (рис. 1) и п л а н е т а р н ы е.
1.2 Основы теории зубчатого зацепления
Профили зубьев пары колес должны быть сопряженными, т. е. заданному профилю зуба одного колеса должен соответствовать вполне определенный профиль зуба другого колеса. Чтобы обеспечить постоянство передаточного числа, профили зубьев нужно очертить такими кривыми, которые удовлетворяли бы требованиям основной теоремы зацепления.
Рис. 6. Схема к доказательству основной теоремы зацепления
Основная теорема зацепления. Для доказательства теоремы рассмотрим пару сопряженных зубьев в зацеплении (рис. 6). Профили зубьев шестерни и колеса касаются в точке S, называемой т о ч к о й з а ц е п л е н и я. Центры вращения О 1 и О 2 расположены на неизменном расстоянии a w друг от друга. Зуб шестерни, вращаясь с угловой скоростью w 1 , оказывает силовое действие на зуб колеса, сообщая последнему угловую скорость w 2 . Проведем через точку S общую для обоих профилей касательную ТТ и нормаль NN. Окружные скорости точки S относительно центров вращения О 1 и О 2:
v 1 = O 1 S w 1 и v 2 = O 2 S w 2
Разложим v 1 и v 2 на составляющие v" 1 и v" 2 по направлению нормали NN и составляющие v"" 1 и v"" 2 по направлению касательной ТТ. Для обеспечения постоянного касания профилей необходимо соблюдение условия v" 1 = v" 2 , в противном случае при v" 1 v" 2 произойдет врезание зубьев. Опустим из центров O 1 и О 2 перпендикуляры O 1 B и О 2 С на нормаль NN.
Из подобия треугольников aeS и BSO 1 v" 1 / v 2 = O 1 B / O 1 S,
Из подобия треугольников afS и CS0 2 v" 2 / v 2 = O 2 C / O 2 S, откуда v" 2 = (v 2 /0 2 S) O 2 C = w 2 *O 2 C. Ho v" 1 = v" 2 , следовательно, w 1 * O 1 B = w 2 * O 2 C.
П е р е д а т о ч н о е ч и с л о
u = w 1 / w 2 = O 2 C / O 1 B. (1)
Нормаль NN пересекает линию центров О 1 О 2 в точке П, называемой п о л ю с о м з а ц е п л е н и я. Из подобия треугольников О 2 ПС и О 1 ПВ
O 2 C / O 1 B = O 2 П / O 1 П = r w1 / r w2 (2)
Сравнивая отношения (1) и (2), получаем
Таким образом, основная теорема зацепления формулируется: для обеспечения постоянного передаточного числа зубчатых колес профили их зубьев должны очерчиваться по кривым, у которых общая нормаль NN , проведенная через точку касания профилей, делит расстояние между центрами O 1 O 2 на части, обратно пропорциональные угловым скоростям.
Полюс зацепления П сохраняет неизменное положение на линии центров O 1 O 2 , следовательно, радиусы r w 1 и r w 2 также неизменны.
Окружности радиусов r w 1 и r w 2 называют н а ч а л ь н ы м и. При вращении зубчатых колес начальные окружности перекатываютсяч друг по другу без скольжения, о чем свидетельствует равенство их окружных скоростей w 1 r w 1 = w 2 r w 2 , полученное из формулы (3).
Из множества кривых, удовлетворяющих требованиям основной теоремы зацепления, практическое применение в современном машиностроении получила э в о л ь в е н т а о к р у ж н о с т и, которая:
а) позволяет сравнительно просто и точно получить профиль зуба в процессе нарезания;
б) без нарушения правильности зацепления допускает некоторое изменение межосевого расстояния a w (это изменение может возникнуть в результате неточностей изготовления и сборки).
Эвольвента окружности (рис. 8.7). Эвольвентой окружности называют кривую, которую описывает точка S прямой NN, перекатываемой без скольжения по окружности радиуса г b . Эта окружность называется эволютой или о с н о в н о й о к р у ж н о с т ь ю, а перекатываемая прямая NN - п р о и з в о д я щ е й п р я м о й.
Характер эвольвентного зубчатого зацепления определяется свойствами эвольвенты.
Производящая прямая NN является одновременно касательной к основной окружности и нормалью ко всем производимым ею эвольвентам.
Две эвольвенты одной и той же основной окружности эквидистантны *.
С увеличением радиуса r b основной окружности эвольвента становится более пологой и при r b → ∞ обращается в прямую.
Радиус кривизны эвольвенты в точке S 2 равен длине дуги S 0 B основной окружности. Центр кривизны эвольвенты в данной точке находится на основной окружности.
1.3 Изготовление зубчатых колес
Заготовки зубчатых колес получают литьем, ковкой в штампах или свободной ковкой в зависимости от материала, формы и размеров. Зубья колес изготовляют накатыванием, нарезанием, реже литьем.
Накатывание зубьев . Применяется в массовом производстве . Предварительное формообразование зубьев цилиндрических и конических колес производится г о р я ч и м н а к а т ы в а н и е м. Венец стальной заготовки нагревают токами высокой частоты до температуры ~ 1200 °С, а затем обкатывают между колесами-накатниками. При этом на венце выдавливаются зубья. Для получения колес более высокой точности производят последующую механическую обработку зубьев или холодное накатывание - калибровку.
Х о л о д н о е н а к а т ы в а н и е зубьев применяется при модуле до 1 мм. Зубонакатывание - высокопроизводительный метод изготовления колес, резко сокращающий отход металла в стружку.
Нарезание зубьев . Существует два метода нарезания зубьев: копирование и обкатка. М е т о д к о п и р о в а н и я заключается в прорезании впадин между зубьями модульными фрезами (рис. 8): дисковыми (а) или пальцевыми (б). После прореза-ния каждой впадины заготовку поворачивают на шаг зацепления. Профиль впадины представляет собой копию профиля режущих кромок фрезы, отсюда и название - метод копирования. Метод копирования - малопроизводительный и неточный, применяется преимущественно в ремонтном деле.
Рис. 7. Схема нарезания
зубьев методом
обкатки
Нарезание зубьев м е т о д о м о б к а т к и основано на воспроизведении зацепления зубчатой пары, одним из элементов которой является режущий инструмент - червячная фреза (рис. 9, а), долбяк (рис.9, б) или реечный долбяк - гребенка (см. рис. 7). Червячная фреза имеет в осевом сечении

форму инструментальной рейки. При нарезании зубьев заготовка и фреза вращаются вокруг своих осей, обеспечивая непрерывность процесса.
Нарезание зубьев червячными фрезами широко применяют для изготовления
цилиндрических колес с внешним расположени ем зубьев. Для нарезания колес с внутренним расположением зубьев применяют долбяки. Гребенками нарезают прямозубые и косозубые колеса с большим модулем зацепления.
Нарезание зубьев конических колес методом обкатки производится строганием (рис. 10, а), фрезерованием (рис. 10, б), инструментом с прямобочным профилем или резцовыми головками.
Отделка зубьев. Зубья точных зубчатых колес после нарезания подвергают отделке шевингованием, шлифованием, притиркой или обкаткой.
Ш е в и н г о в а н и е применяют для тонкой обработки неза каленных колес. Выполняют инструментом - шевером, имеющим вид зубчатого колеса с узкими канавками на поверхности зубьев. Вращаясь в зацеплении с обрабатываемым колесом, шевер снимает режущими кромками канавок волосообразные стружки с зубьев колеса.
Ш л и ф о в а н и е применяют для обработки закаленных зубьев. Выполняют шлифовальными кругами способом копирования или обкатки.
П р и т и р к у используют для отделки закаленных зубьев колес. Выполняют притиром – чугунным точно изготовленным колесом с использованием притирочных абразивных паст.
О б к а т к а применяется для сглаживания шероховатостей на рабочих поверхностях зубьев незакаленных колес. В течение 1…2 мин зубчатое колесо обкатывается под нагрузкой с эталонным колесом большой твердости.
1.4 Материалы зубчатых колес
Выбор материала зубчатых колес зависит от назначения передачи и условий ее работы. В качестве материалов колес применяют стали, чугуны и пластмассы.
Стали. Основными материалами для зубчатых колес служат термически обрабатываемые стали. В зависимости от твердости стальные зубчатые колеса делятся на две группы.
П е р в а я г р у п п а - колеса с твердостью поверхностей зубьев Н ≤ 350 НВ. Применяются в слабо- и средненагруженных передачах. Материалами для колес этой группы служат углеродистые стали 35, 40, 45, 50, 50Г, легированные стали 40Х, 45Х, 40ХН и др. Термообработку - улучшение производят до нарезания зубьев. Колеса при твердости поверхностей зубьев Н ≤ 350 НВ хорошо прирабатываются и не подвержены хрупкому разрушению.
Для равномерного изнашивания зубьев и лучшей их прираба-тываемости твердость шестерни прямозубой передачи должна быть на (25...50) НВ больше твердости колеса.
Для косозубых передач твердость НВ рабочих поверхностей зубьев шестерни желательна возможно большая.
В т о р а я г р у п п а - колеса с твердостью поверхностей Н>350 НВ. Высокая твердость рабочих поверхностей зубьев достигается объемной и поверхностной закалкой, цементацией, азотированием, цианированием. Эти виды термообработки позволяют в несколько раз повысить нагрузочную способность передачи по сравнению с улучшенными сталями.
Зубья колес с твердостью поверхностей Н>350 НВ не прирабатываются. Для неприрабатывающихся зубчатых передач обеспечивать разность твердостей зубьев шестерни и колеса не требуется.
П о в е р х н о с т н а я з а к а л к а зубьев с нагревом токами высокой частоты (т.в.ч.) целесообразна для шестерен с модулем m ≥ 2 мм, работающих с улучшенными колесами, ввиду хорошей приработке зубьев. При малых модулях мелкий зуб прокаливается насквозь, что делает его хрупким и сопровождается короблением. Для закалки т.в.ч. используют стали 45, 40Х, 40ХН, 35ХМ.
Ц е м е н т а ц и ю применяют для колес, размеры которых должны быть минимальные (авиация, транспорт и т.п.). Для цементации используют стали 20Х, 12ХН3А и др.
А з о т и р о в а н и е обеспечивает особо высокую твердость поверхностных слоев зубьев. Для передач, в которых отсутствует абразивное изнашивание зубьев, можно применять азотирование. Оно сопровождается малым короблением и позволяет получать зубья 7-й степени точности без отделочных операций. Для повышения прочности сердцевины зуба заготовку колеса подвергают улучшению. Для азотирования применяют стали 40ХНМА, 40Х2НМА, 38ХМЮА, 38Х2Ю.
Колеса с твердостью Н > 350 НВ нарезают до термообработки. Отделку зубьев производят после тармообработки.
Выбор марок сталей для зубчатых колес. Без термической обработки механические характеристики всех сталей близки, поэтомуприменение легированных сталей без термообработки недопустимо.
Прокаливаемость сталей различа:
высоколегированных – наибольшая,
углеродистых – наименьшая. Стали с
плохой прокаливавемостью при больших
сечениях заготовок нельзя термически
обработать на высокую твердость. Поэтому
марку стали для зубчатых
колес выбирают с учетом размеров их
заготовок.
Характеристики сталей зависят не только от химического состава и вида термообработки, но также и от предельных размеров заготовок: диаметра заготовки шестерни или червяка D npe д и наибольшей толщины сечения заготовки колеса S пред.
Стальное литье. Применяют при изготовлении крупных зубчатых колес (d a ≥ 500 мм). Употребляют стали 35Л...55Л. Литые колеса подвергают нормализации.
Чугуны. Применяют при изготовлении зубчатых колес тихоходных открытых передач. Рекомендуются чугуны СЧ18...СЧ35. Зубья чугунных колес хорошо прирабатываются, но имеют пониженную прочность на изгиб.
Пластмассы. Применяют в быстроходных слабонагруженных передачах для шестерен, работающих в паре с металлическими колесами. Зубчатые колеса из пластмасс отличаются бесшумностью и плавностью хода. Наиболее распространены текстолит, лигнофоль, капролон, полиформальдегид.
1.5. Виды разрушения зубьев и критерии работоспособности зубчатых передач
В процессе работы на зубья действуют силы передаваемой нагрузки и силы трения. Для каждого зуба напряжения изменяются во времени по прерывистому отнулевому циклу. Повторно-переменные напряжения являются причиной усталостного разрушения зубьев: их поломки и выкрашивания рабочих поверхностей. Трение в зацеплении вызывает изнашивание и заедание зубьев.
Поломка зубьев. Это наиболее опасный вид разрушения. Излом зубьев является следствием возникающих в зубьях повторно-переменных напряжении изгиба и перегрузки. Усталостные трещины образуются у основания зуба на той стороне, где от изгиба возникают наибольшие
напряжения растяжения. Прямые короткие зубья выламываются полностью, а длинные, особенно косые, обламываются по косому сечению (рис. 12, а). Усталостную поломку предупреждают расчетом на прочность по напряжениям изгиба σ f , применением коррекции, а также увеличением точности изготовления и монтажа передачи.
Усталостное выкрашивание рабочих поверхностей зубьев. Основной вид разрушения зубьев для большинства закрытых передач. Возникает вследствие действия повторно-переменных контактных напряжений σ н. Разрушение начинается на ножке зуба в околополюсной зоне, где развивается наибольшая сила трения, способствующая пластическому течению металла и образованию микротрещин на поверхности зубьев. Развитию трещин способствует расклинивающнй эффект смазочного материала, который запрессовывается и трещины зубьев при зацеплении. Развитие трещин приводит к выкрашиванию частиц поверхности, образованию вначале мелких ямок (рис. 12, б), переходящих далее в раковины. При выкрашивании нарушаются условия образования сплошной масляной пленки (масло выжимается в ямки), что приводит к быстрому изнашиванию и задиру зубьев. Возрастают динамические нагрузки, шум, температура.
При твердости поверхностей зубьев Н блюдаться ограниченное выкрашивание, возникающее лишь на участках с концентрацией напряжений. После приработки зубьев такое выкрашивание прекратится.
Прогрессирующее выкрашивание возникает при твердости поверхности зубьев Н > 350 НВ, оно постепенно поражает всю рабочую поверхность ножек зубьев.
Усталостное выкрашивание зубьев предупреждают расчетом на прочность по контактным напряжениям, повышением твердости поверхности зубьев, применением коррекции, повышением степени точности, правильным выбором сорта масла.
В открытых передачах выкрашивания не наблюдается, так как изнашивание поверхности зубьев опережает развитие усталостных трещин.
Изнашивание зубьев. Основной вид разрушения зубьев открытых передач. По мере изнашивания зуб утоняется (рис. 12, в), ослабляется его ножка, увеличиваются зазоры в зацеплении, что в конечном счете приводит к поломке зубьев. Разрушению зубьев предшествует возникновение повышенного шума при работе передачи. Изнашивание можно уменьшить защитой от попадания абразивных частиц, повышением твердости и понижением шероховатости рабочих поверхностей зубьев, уменьшением скольжения зубьев путем коррекции.
Заедание зубьев . Заключается в приваривании частиц одного зуба к другому вследствие местного повышения температур в зоне зацепления. Образовавшиеся наросты на зубьях задирают рабочие поверхности других зубьев, бороздя их в направлении скольжения (рис. 12, г). Заедание зубьев предупреждают повышением твердости и понижением шероховатости рабочих поверхностей зубьев, применением коррекции, правильным подбором противозадирных масел.
2 ЦИЛИНДРИЧЕСКИЕ КОСОЗУБЫЕ ПЕРЕДАЧИ
1.1 Общие сведения
Цилиндрические колеса, у которых зубья расположены по винтовым линиям на делительном цилиндре, называют к о с о з у б ы м и (см. рис. 1, б). В отличие от прямозубой в косозубой передаче зубья входят в зацепление не сразу по всей длине, а постепенно. Увеличивается время контакта одной пары зубьев, в течение которого входят новые пары зубьев, нагрузка передается по большому числу контактных линий, что значительно снижает шум и динамические нагрузки.
Чем
больше угол наклона линии зуба β,
тем выше плавность зацепления. У пары
сопряженных косозубых колес
с внешним
зацеплением углы β
равны, но противоположны по направлению.
Если к передачам не предъявляют специальных требований, то колеса нарезают правыми, а шестерни - левыми.
У косозубого колеса (рис. 13) расстояние между зубьями можно измерить в торцовом, или окружном (t – t ) , и нормальном (п – n ) направлениях. В первом случае получим окружной шаг p t , во втором - нормальный шаг р. Различными в этих направлениях будут и модули зацепления:
Рис. 13. Геометрические размеры
косозубого колеса
где m t и m - окружной и нормальный модули зубьев.
Согласно рис. 13
следовательно,
где β - угол наклона зуба на делительном цилиндре.
Нормальный модуль m должен соответствовать стандарту и являться исходной величиной при геометрических расчетах.
Делительный и начальный диаметры
Косозубое колесо нарезают тем же инструментом, что и прямозубые. Наклон зуба получают поворотом инструмента на угол β. Профиль косого зуба в нормальном сечении соответствует исходному контуру инструментальной рейки и, следовательно, совпадает с профилем прямого зуба модуля т.
Высоты головки косого зуба h a и ножки h f соответственно равны:
Диаметр вершин
Межосевое расстояние
В косозубой передаче, меняя значение угла β, можно незначительно изменить а w .
Прямозубую передачу можно рассматривать как частный случай косозубой, у которой которой β = 0
1.2 Эквивалентное колесо
Как указывалось выше, профиль косого зуба в нормальном сечении А - А (рис. 14) соответствует исходному контуру инструментальной рейки и, следовательно, совпадает с профилем прямозубого колеса. Расчет косозубых колес ведут, используя параметры эквивалентного прямозубого колеса.

Делительная окружность косозубого колеса в нормальном сечении А - А (см. рис. 14) образует эллипс, радиус кривизны которого в полюсе зацепления
Профиль зуба в этом сечении почти совпадает с профилем условного прямозубого колеса, называемого эквивалентным, делительный диаметр которого
d v = 2 p v = d / cos 2 β = m t z / cos 2 β = mz / cos 3 β = mz v ,
откуда э к в и в а л е н т н о е ч и с л о з у б ь е в
где z – действительное число зубьев косозубого колеса.
Из этой формулы следует, что с увеличением β возрастает z v .
1.3. Силы в зацеплении
В косозубой передаче нормальная сила F n составляет угол β с торцом колеса (рис. 15). Разложив F n на составляющие, получим:
радиальную силу
где F t = 2T 2 / d 2 - окружная сила;
осевую силу
При определении направлений сил учитывают направление вращения колес и направление наклона зуба (правое или левое).
Осевая сила F a дополнительно нагружает подшипники, возрастая с увеличением β. По этой причине для косозубых колес принимают β = 8...18°. Наличие в зацеплении осевых сил является недостатком косозубой передачи.
1.4. Расчет на контактную прочность
Вследствие наклонного расположения зубьев в косозубом зацеплении одновременно находится несколько пар зубьев, что уменьшает нагрузку на один зуб, повышая его прочность. Наклонное расположение зубьев уменьшает динамические нагрузки. Все эти особенности трудно учесть при выводе расчетных формул, поэтому расчет на прочность косозубых передач ведут по формулам эквивалентных прямозубых передач с введением в них поправочных коэффициентов. По условиям прочности габариты косозубых передач получаются меньше, чем прямозубых.
Проектировочный расчет. Аналогично расчету прямозубой передачи межосевое расстояние для стальной косозубой пары
где Т 2 - в Н * мм; [ σ] н - в Н / мм 2 .
Проверочный расчет. Аналогично расчету прямозубой передачи контактные напряжения в поверхностном слое косых зубьев
где дополнительно по стандарту:
Z H ≈ 1,76 cos β - коэффициент, учитывающий форму сопряженных поверхностей зубьев. Среднее значение Z H ≈ 1,71;
Коэффициент, учитывающий перекрытие зубьев. Среднее значение Z ε ≈ 0,8;
Z М = 275 Н 1/2 /мм - для стальных колес.
Следовательно,
где F t - в Н; d 2 , b 2 - в мм; K H α - коэффициент, учитывающий распределение нагрузки между зубьями. Для косозубых колес 7...8-й степени точности:
К Н α = 1,04...1,09 при υ ≤5 м/с,
К Н α = 1,07...1,13 при υ = 5...10 м/с;
К Н β - коэффициент неравномерности нагрузки по ширине венца;
К Н υ - коэффициент динамической нагрузки. Для косозубых передач рекомендуется:
К Н υ = 1,02...1,06 при любой твердости зубьев и υ ≤ 10 м/с,
К Н υ = 1,1 при твердости зубьев Н ≤ 350 НВ и υ = 10...20 м/с,
К Н υ = 1,05 при твердости зубьев Н > 350 НВ и υ = 10...20 м/с.
1.5. Расчет на изгиб
Аналогично расчету прямозубой передачи условия прочности на изгиб зубьев шестерни и колеса косозубой передачи
где Y F - коэффициент формы зуба, выбирают по эквивалентному числу зубьев z v ;
Y β = 1 - β /140° - коэффициент, учитывающий наклон зуба;
К Fa - коэффициент, учитывающий распределение нагрузки между зубьями. Для косозубых колес при υ ≤ 10 м/с и 7...8-й степеней точности К Fa = 0,81...0,91;
К F β - коэффициент, учитывающий распределение нагрузки по ширине венца;
К F υ - коэффициент, учитывающий динамическую нагрузку в зацеплении. Для косозубых передач при υ ≤ 10 м/с:
К F υ = 1,2 при твердости зубьев колеса Н ≤ 350 НВ,
К F υ = 1,l при твердости зубьев колеса Н > 350 НВ.
1.7 Шевронные цилиндрические передачи
Шевронное колесо представляет собой сдвоенное косозубое колесо, выполненное как одно целое (см. рис. 1, в). Вследствие разного направления зубьев на полушевронах осевые силы F a /2 взаимно уравновешиваются на колесе и на подшипники не передаются (рис. 16). Это обстоятельство позволяет принимать у шевронных колес угол наклона зуба β = 25...40°, что повышает прочность зубьев и плавность передачи.
Шевронные зубчатые
колеса изготовляют с дорожкой в середине
колеса для выхода режущего инструмента
(червячной фрезы на рис. 16) или без
дорожки (нарезаются долбяком или
гребенкой со специальной заточкой, см.
рис. 1, в).
Шевронные колеса без дорожки нарезают на специальных малопроизводительных и дорогих станках, поэтому их применяют реже, чем колеса с дорожкой. Ширина дорожки а = (10...15) m .
Шевронный зуб требует строго определенного осевого положения шестерни относительно колеса, поэтому пары монтируют в подшипниках, допускающих осевую «игру» вала.
Недостатком шевронных колес является большая стоимость их изготовления. Применяются в мощных быстроходных закрытых передачах.
Геометрический и прочностной расчет шевронной передачи аналогичны расчетам косозубой передачи. Для шевронной передачи коэффициент ширины обода колеса ψ а = 0,4…0,8.
При строгой параллельности зубьев и осей О 2 О 2 и O 1 O 1 прямые зубья входят в зацепление по всей длине В (рис. 17, а)
Если колесо шириной
В
,
имеющее прямые зубья, разрезать нa
ряд тонких колес 1,
2, 3, 4, 5
(рис.
17, б) и каждое из них повернуть на оси
относительно предыдущего на некоторый
угол, чтобы зуб сместился на дугу s,
то получится колесо со ступенчатым
зубом. При вращении колес в зацепление
последовательно" >удут входить
участки 1
- 1,
2-2, 3
- 3
и т. д. В такой же последовательности
они будут и выходить из зацепления.
Взяв бесконечно большое число бесконечно тонких колес, получим косой (винтовой) зуб, наклоненный к оси вращения под углом β (рис. 17, в). Косые зубья работают более плавно по сравнению с прямыми зубьями, так как одновременно в зацеплении находится большее число зубьев при той же ширине колес В . Существенным недостатком косозубых колес является наличие осевого усилия Р ос , стремящегося
сдвинуть
колеса вдоль оси вала. Из рис. 17, в
видно, что
чем больше будет угол β,
тем больше будет и
осевое
усилие Р
ос
при одном
и том же окружном усилии Р
0кр
.
На рис. 17, в
показано
направление давления зуба шестерни на
зуб колеса.
Для исключения осевой нагрузки на опоры на валу устанавливают два косозубых колеса с наклоном зубьев в противоположные стороны. При этом следует иметь в виду, что при неточной продольной установке колес на валу может оказаться, что будет соприкасаться только одна пара зубьев из двух сопряженных пар колес, например левая, как показано на рис. 18 (как правило, один из валов делают самоустанавливающимся относительно другого).
Осевая сила Р ос стремится сдвинуть влево вал вместе с закрепленным на нем колесом. Для распределения окружного усилия Р окр поровну на оба колеса необходимо предусмотреть
продольный так называемый монтажный зазор е между опооой и бортиком вала.
После сдвига шестерни (и вала) влево под действием силы Р ос давление на обе половины колеса и шестерни распределяется поровну.
1.8 Зубчатые передачи с зацеплением М. Л. Новикова
Эвольвентное
зацепление
, распространенное
в современном машиностроении, является
л и н е й ч а т ы м, так как контакт зубьев
происходит по линии (практически по
узкой площадке), расположенной вдоль
зуба (рис. 19). Вследствие малого приведенного
радиуса кривизны контактная прочность
эвольвентного зацепления сравнительно
невысока, поэтому для современных мощных
передач важен вопрос повышения несущей
способности зубчатых передач.
М.Л.
Новиковым было предложено новое т о ч
е ч н о е з а ц е п л е н и е, в
котором профили зубьев колес в торцовом
сечении очерчены по дугам окружности
(рис. 20). Зуб шестерни делается выпуклым,
а зуб колеса - вогнутым, что увеличивает
их приведенный радиус кривизны,
значительно повышая контактную прочность
передачи.
В
зацеплении Новикова контакт зубьев
происходит в точке
и зубья
касаются только в момент прохождения
профилей через эту точку (рис. 20), а
непрерывность передачи движения
обеспечивается винтовой формой зубьев.
Поэтому зацепление Новикова
может быть только косозубым
с углом наклона зубьев
ß=15...20°
. Положение
точки контакта зубьев характеризуется
ее смещением от полюса,
а
линия зацепления располагается
параллельно оси колеса. В результате
упругой деформации и приработки под
нагрузкой точечный контакт переходит
в контакт по малой площадке (рис. 20). При
взаимном перекатывании зубьев контактная
площадка перемещается вдоль зуба с
большой скоростью, превышающей окружную
скорость колес примерно в три раза, что
создает благоприятные условия для
образования устойчивого масляного слоя
между зубьями. По этой причине потери
на трение в передаче Новикова значительно
меньше.
Применяют
передачи Новикова с одной линией
зацепления - заполюсные (реже -
дополюсные) и с двумя линиями зацепления
- дозаполюсные. В передачах с одной
линией зацепления профиль зуба одного
колеса (как правило, шестерни) выпуклый
(см. рис. 20), а другого-вогнутый. Если
ведущим звеном является шестерня с
выпуклым профилем зубьев, то точка
контакта расположена за полюсом и
передачу называют з а п о л ю с н о й. Если
ведущим является колесо с вогнутым
профилем, то передача становится
д о п о л ю с н о й.
Д о з а п о л ю с н у ю передачу (рис.21) можно представить как сочетание дополюсной и заполюсной передач. Головки зубьев шестерни и колеса имеют выпуклый профиль, а ножки - вогнутый. Эта передача обладает большей контактной и изгибной прочностью.
Для нарезания выпуклых и вогнутых зубьев заполюсной (дополюсной) передачи требуются разные инструменты. Зубья дозаполюсной передачи нарезают одним инструментом.
Существенным н е д о с т а т к о м зацепления Новикова является повышенная чувствительность к изменению межосевого расстояния и колебаниям нагрузок.
Расчет передач с зацеплением Новикова ведут аналогично расчету передач с эвольвентным зацеплением, но с учетом их особенностей.
3. СПИСОК ЛИТЕРАТУРЫ:
Н. Г. Куклин, Г. С. Куклина, «Детали машин». Москва, Высшая школа, 1987г.
Я. М. Павлов, «Детали машин». Ленинград, Издательство «Машиностроение», 1969г.
Лабораторная работа №1
АНАЛИЗ КОНСТРУКЦИИ ЗУБЧАТЫХ КОЛЕС И ОПРЕДЕЛЕНИЕ ИХ ПАРАМЕТРОВ
Назначение и классификация зубчатых колес
Назначение зубчатого колеса : передача вращательного движения и крутящего момента от сопряженного колеса на вал или с вала на сопряженное колесо с обеспечением заданных нагрузочных и скоростных параметров в течение заданного срока эксплуатации.
Зубчатые колеса используют так же в реечных передачах , которые предназначены для преобразования вращательного движения в поступательное или наоборот.
^ Зубчатые колеса классифицируют :
- по типу передачи – цилиндрические и конические;
- по типу зубьев
– прямозубые, косозубые, шевронные и с криволинейными зубьями. (Рис 1, 2);
Рис 1. Примеры цилиндрических зубчатых передач с внешним и внутренним зацеплением
- по расположению зубьев
– с внешним и внутренним зацеплением (Рис 1);
- по конструктивному исполнению – колеса, изготовленные совместно с валом и называемые вал-шестерня (Рис.3.) и автономные (Рис.4.) В последнем случае вал и зубчатое колесо изготавливают отдельно, затем монтируют совместно в одну сборочную единицу за счет специальных соединений (чаще всего шпоночных или шлицевых ) таким образом, чтобы колесо не имело возможности поворота вокруг вала. В таком состоянии при эксплуатации передачи колесо и вал могут взаимно передавать крутящие моменты.
Косозубые колеса классифицируют по направлению зубьев – с правым и левым направлением. Для определения направления нужно посмотреть вдоль зуба в верхней части косозубого колеса . Если по направлению взгляда зуб отклоняется вправо, то соответственно направление зуба правое и наоборот.
Рис.2. Конические зубчатые передачи с прямыми (а.) и криволинейными (б.) зубьями;
в - реечная передача с прямыми зубьями
Рис. 3. Зубчатое колесо, изготовленное совместно с валом
2. Конструктивные исполнения цилиндрических зубчатых колес
Основными конструктивными элементами зубчатого колеса являются:
- обод, на котором нарезаны или накатаны зубья;
- ступица , закрепляемая на валу,
- диск , соединяющий обод со ступицей. В диске могут выполняться отверстия для уменьшения массы и момента инерции колес (Рис. 4 в, г).
В частных случаях:
Обод, диск и ступица объединены в одну конструкцию (Рис. 4 а).
Выполнены заодно только обод и диск (Рис. 4 б).
Рис. 4. Конструктивные элементы автономных зубчатых колес:
а – только обод; б – обод и ступица; в – обод, диск и ступица (толщина диска равна ширине обода); г - обод, диск и ступица
^
3. Материалы и технологии изготовления зубчатых колес
Зубчатые колеса в большинстве случаев изготавливают из сталей. Реже из чугунов, полимерных материалов и цветных металлов . Колеса из сталей используют как в открытых, так и в закрытых передачах относительно высокой мощности. Для изготовления колес открытых передач при окружной скорости до 6 м/с используют высокопрочный чугун. Колеса тихоходных и малонагруженных открытых передач можно изготавливать из серого чугуна. Колеса из полимерных материалов применяют в малонагруженных передачах, когда необходимо обеспечить бесшумную работу, так как эти материалы обладают высокими демпфирующими свойствами, т. е. способны поглощать энергию ударов.
Производство стальных зубчатых колес может быть организовано в одну или две стадии. Одностадийное производство – это механическая обработка готового проката (прутка). В две стадии вначале изготавливают стальную заготовку методами свободной ковки, объемной штамповки или литья, затем проводят ее механическую обработку. Для повышения эксплуатационных свойств материалы колес подвергают термической или термохимической обработке: улучшению, закалке, цементации или азотированию. Улучшение проводят в объеме заготовки до ее механической обработки; закалку, цементацию и азотирование - рабочих поверхностей зубьев после их нарезки. Способ изготовления стальных колес определяется их размерами и программой выпуска. Колеса диаметром до 200 мм чаще всего изготавливают механической обработкой из прутка. На боковых плоских поверхностях таких изделий отчетливо различимы канавки, образованные в результате проходов токарного резца. Колеса диаметром от 200 до 500 мм чаще всего изготавливают с использованием кованых или штампованных заготовок. Боковые поверхности таких колес, не подвергнутые механической обработке, имеют однородную чистоту обработки без явно выраженных неровностей, так как она соответствует чистоте обработки формообразующего инструмента штампа. При больших диаметрах (более 500 мм) колеса изготавливают литыми. При малых тиражах выпуска или в индивидуальном производстве для изготовления слабонагруженных металлических колес любых размеров могут использоваться заготовки, отформованные литьем. При этом шероховатость боковых поверхностей относительно высока, так как она определяется контактом металлического расплава с формовочной смесью, основным компонентом которой является песок.
Независимо от способа получения заготовки зубья на колесах получают способами нарезания или горячей накатки. Последний способ наиболее экономичен, позволяет повысить изгибную прочность зубьев, но снижает их размерную точность.
Технологические приемы изготовления зубчатых колес из полимерных материалов наиболее производительны и экономичны, так как окончательное формообразование изделия реализуется за одну операцию. Такими операциями являются: литье под давлением из термопластичных материалов и прессование из термореактивных. Конфигурация оформляющей полости технологической оснастки полностью соответствует конфигурации зубчатого колеса с обеспечением высокой чистоты обработки по всей поверхности. Вместе с тем эксплуатация такой дорогостоящей оснастки и соответствующего формующего оборудования экономически оправданы только при больших тиражах выпуска деталей для низконагруженных передач. Вместе с тем в последние годы интенсивно развивается индустрия композиционных материалов на полимерной основе , содержащих высокопрочные волокна, сухие смазки, добавки, устраняющие хрупкость материала и др. Рецептура таких материалов, как правило, соответствует условиям эксплуатации изделия.
Однако стоимость полимерных композиционных материалов значительно выше стоимости металлов. Поэтому из композиционных материалов на полимерной основе изготавливают зубчатые колеса в основном малой массы в конструкциях приборов точной механики и бытовой техники. Зубчатые передачи из полимерных материалов могут работать без смазки, поэтому они успешно применяются в оборудования пищевой промышленности.
^
В инженерной практике решаются две задачи:
Анализ существующего механизма, когда требуются измерения его геометрических параметров;
В данной работе рассматриваются элементы, как анализа, так и синтеза, применительно к колесам зубчатых передач.
Максимальная мощность, передаваемая зубчатой передачей, в значительной степени зависит от двух параметров: высоты зубьев H и делительных диаметров колес d . Оба эти параметра одновременно учитывает основная характеристика передачи – ее модуль:
,
где z – число зубьев колеса. Чем крупнее зубья, тем меньше их количество при постоянном значении d и тем выше модуль.
Предварительное значение модуля m " можно определить через высоту зуба H :
Для цилиндрических колес m " = H / 2,5 .
Ниже приведены ряды значений стандартного модуля m , наиболее часто применяемых в машиностроении (в реальном промышленном проектировании 1-й ряд предпочитают второму):
1-й ряд: 1; 1,25; 1,5; 2; 2,5; 3; 4; 5; 6; 8; 10; 12; 16; 20; 25; 32; 40 мм.
2-й ряд: 1,125; 1,375; 1,75; 2,25; 2,75; 3,5; 4,5; 5,5; 7; 9; 11; 14; 18; 22; 28; 36; 45 мм.
В настоящей работе величину модуля m " следует уточнить по стандарту и принять значение m ближайшее большее из любого указанного ряда.
При известных значениях параметров z и d модуль m " определяют из выражения:
d = m ∙ z .
Диаметр делительной окружности колеса d измерить невозможно. Поэтому с помощью измерительных устройств, например, штангенциркулем, оценивают диаметр вершин зубьев d a и диаметр впадин d f . При заранее заданных параметрах делительного диаметра и модуля расчетные значения d a и d f определяют из выражений:
d a = d + 2∙ m ; d f = d – 2,4∙ m .
Для косозубых колес угол наклона зуба β (Рис. 5) можно определить по зависимости:
β = arccos ((m ∙ z)/(d – 2,4∙m)) .
Рис. 5 Сечение зубчатого венца по дуге делительной окружности А - Б
При зацеплении зубчатых колес обод воспринимает нагрузку от зубьев. Поэтому его толщина q
должна быть достаточной, чтобы обеспечить как его прочность и жесткость, так и податливость. Податливость способствует равномерному распределению нагрузки между зубьями и по длине каждого зуба. Рекомендуется выполнять толщину обода в соответствии с формулой:
q = (2,5…4,0) ∙ m , но не менее 8 мм.
Тогда внутренний диаметр обода D 0 будет определяться из выражения:
D 0 = d f - 2 q .
Ступица служит для соединения колеса с валом и передачи вращающего момента, а ее торцы определяют положение колеса по длине вала. Для передачи вращающего момента отверстие d вал в ступице выполняют либо с посадкой с натягом либо со шпоночными или шлицевыми пазами (Рис 6). Размеры пазов зависят от диаметра вала, определяются стандартом и приведены в таблице 1.
Рис 6 Шпоночное соединение
Таблица 1
Размеры сечений шпонок и пазов, мм, по ГОСТ 8788-68 *
(В таблице: b – ширина шпонки и соответственно шпоночного паза; h – высота шпонки.)
Длина ступицы L с m должна быть достаточной, чтобы обеспечить монтаж зубчатого колеса на валу без перекоса и работоспособность соединения ступицы с валом. Рекомендуется выполнять длину ступицы равной:
L с m = (0,8…1,5) ∙ d вал ,
но не менее ширины обода в , т.е. L с m ≥ в . Диаметр ступицы d с m принимают достаточным для обеспечения прочности и надежности соединения по выражению:
d с m = 1,8 ∙ d вал .
Толщина диска С должна быть достаточной, чтобы обеспечить жесткость колеса, и определяется в зависимости от способа его изготовления. Рекомендуется выполнять толщину диска у цилиндрических колес:
Кованых и штампованных C = 0,3 · в ;
Литых С = 0,2 ∙ в.
d отв = 0,25 ∙(D 0 - d с m ).
а располагать их на диаметре
D отв = 0,5 ∙(D 0 + d с m ).
На торцах обода и ступицы выполняют фаски, размер которых n × 45°. Параметр n определяется из выражения:
n = (0,5…0,7) ∙ m .
Сопряжение обода и диска, диска и ступицы выполняют по радиусу r , величина которого принимается в зависимости от диаметра колеса:
при d а ≤ 500 мм - r = 5 мм; при d а > 500 мм - r = 7 мм.
Зубчатое колесо должно быть зафиксировано на вале как в окружном, так и в осевом направлениях. Наиболее простым способом фиксации колеса является применение посадок с большим натягом или штифтов (Рис. 6 а ). В этих случаях обеспечивается фиксация колеса в обоих направлениях, Однако использование посадок с натягом связано с большими трудностями при монтаже и демонтаже узла. Поэтому для окружного фиксирования колеса чаще используют шпонки и шлицы. Эти виды соединений существенно облегчают монтаж и демонтаж узла, но требуют дополнительного фиксирования колеса в осевом направлении. В этих случаях осевое фиксирование осуществляется установочными винтами, пружинными кольцами, распорными втулками и т.д. (рис. 7 б, в, г ).
Рис.7. Способы осевого фиксирования колеса: а - штифтом; б - установочным винтом; в - пружинными кольцами; г - распорной втулкой
Порядок измерения параметров и их расчета приведены в бланке отчета о выполнении настоящей работы
В результате изучения студент должен знать:
Область применения зубчатых передач;
- классификацию зубчатых передач.
4.1.1 Роль и значение зубчатых передач в машиностроении
Зубчатые передачи являются наиболее распространёнными типами механических передач . Они находят широкое применение во всех отраслях машиностроения, в частности в металлорежущих станках, автомобилях, тракторах, сельхозмашинах и т.д., в приборостроении, часовой промышленности и др. Их применяют для передачи мощностей от долей до десятков тысяч киловатт при окружных скоростях до 150 м/с и передаточных числах до нескольких сотен и даже тысяч, с диаметром колёс от долей миллиметра до 6 м и более.
Зубчатая передача относиться к передачам зацеплением с непосредственным контактом пары зубчатых колёс. Меньшее из колёс передачи принято называть шестерней, а большее - колесом. Зубчатая передача предназначена в основном для передачи вращательного движения.
4.1.2 Достоинства зубчатых передач
1) высокая нагрузочная способность;
2) малые габариты;
3) большая надёжность и долговечность (40000 ч);
4) постоянство передаточного числа;
5) высокий КПД (до 0,97…0,98 в одной ступени);
6) простота в эксплуатации.
4.1.3 Недостатки зубчатых передач
1) повышенные требования к точности изготовления и монтажа;
2) шум при больших скоростях;
3) высокая жёсткость, не позволяющая компенсировать динамические нагрузки.
4.1.4. Классификация зубчатых передач
1. По взаимному расположению геометрических осей валов различают передачи:br - с параллельными осями - цилиндрические (рис.2.3.1.а-г);
- с пересекающимися осями - конические (рис.2.3.1.д; е);
- со скрещивающимися осями - цилиндрические винтовые (рис.2.3.1.ж);
- конические гипоидные и червячные (рис. 2.3.1.з);
- реечная передача (рис. 2.3.1.и).








Рисунок 2.3.1 Виды зубчатых передач
2. В зависимости от взаимного расположения зубчатых колёс:
- с внутренним зацеплением (направление вращения колёс совпадают).
3. По расположению зубьев на поверхности колёс различают передачи:
- прямозубые; косозубые; шевронные; с круговым зубом.
4. По форме профиля зуба различают передачи:
- эвольвентные;
- с зацеплением М. Л. Новикова;
- циклоидальные.
5. По окружной скорости различают передачи:
- тихоходные ();
- среднескоростные
Зубчатые передачи
Зубчатая передача - Механизм, в котором два подвижных звена являются зубчатыми колесами, образующими с неподвижным звеном вращательную или поступательную пару
Виды зубчатых передач: а, б, в - цилиндрические зубчатые передачи с внешним зацеплением; г - реечная передача; д - цилиндрическая передача с внутренним зацеплением; е - зубчатая винтовая передача; ж, з, и - конические зубчатые передачи; к - гипоидная передача
В большинстве случаев зубчатая передача служит для передачи вращательного движения. В некоторых механизмах эту передачу применяют для преобразования вращательного движения в поступательное. Зубчатые передачи - наиболее распространенный тип передач в современном машиностроении и приборостроении; их применяют в широких диапазонах скоростей (до 100 м/с), мощностей (до десятков тысяч киловатт).
Основные достоинства зубчатых передач по сравнению с другими передачами:
Технологичность, постоянство передаточного числа;
Высокая нагрузочная способность;
Высокий КПД (до 0,97-0,99 для одной пары колес);
Малые габаритные размеры по сравнению с другими видами передач при равных условиях;
Большая надежность в работе, простота обслуживания;
Сравнительно малые нагрузки на валы и опоры.
К недостаткам зубчатых передач следует отнести:
Невозможность бесступенчатого изменения передаточного числа;
Высокие требования к точности изготовления и монтажа;
Шум при больших скоростях; плохие амортизирующие свойства;
Громоздкость при больших расстояниях между осями ведущего и ведомого валов;
Потребность в специальном оборудовании и инструменте для нарезания зубьев;
Зубчатая передача не предохраняет машину от возможных опасных перегрузок.
Зубчатые передачи и колеса классифицируют по следующим признакам (см. рис. 1):
По взаимному расположению осей колес - с параллельными осями (цилиндрические, см. рис. 1, а-д), с пересекающимися осями (конические, см. рис. 1, ж-и), со скрещивающимися осями (винтовые, см. рис. 1, е, к);
По расположению зубьев относительно образующих колес - прямозубые, косозубые, шевронные и с криволинейным зубом;
По конструктивному оформлению - открытые и закрытые;
По окружной скорости - тихоходные (до 3 м/с), для средних скоростей (3-15 м/с), быстроходные (св. 15 м/с);
По числу ступеней - одно- и многоступенчатые;
По расположению зубьев в передаче и колесах - внешнее, внутреннее (см. рис. 1, д) и реечное зацепление (см. рис. 1, г);
По форме профиля зуба - с эвольвентными, круговыми;
По точности зацепления. Стандартом предусмотрено 12 степеней точности. Практически передачи общего машиностроения изготовляют от шестой до десятой степени точности. Передачи, изготовленные по шестой степени точности, используют для наиболее ответственных случаев.
Из перечисленных выше зубчатых передач наибольшее распространение получили цилиндрические прямозубые и косозубые передачи, как наиболее простые в изготовлении и эксплуатации. Преимущественное распространение получили передачи с зубьями эвольвентного профиля, которые изготавливаются массовым методом обкатки на зубофрезерных или зубодолбежных станках. Достоинство эвольвентного зацепления состоит в том, что оно мало чувствительно к колебанию межцентрового расстояния. Другие виды зацепления применяются пока ограниченно. Так, циклоидальное зацепление, при котором возможна работа шестерен с очень малым числом зубьев (2-3), не может быть, к сожалению, изготовлено современным высокопроизводительным методом обкатки, поэтому шестерни этого зацепления трудоемки в изготовлении и дороги; новое пространственное зацепление Новикова пока еще не получило массового распространения, вследствие большой чувствительности к колебаниям межцентрового расстояния.
Прямозубые колёса (около 70%) применяют при невысоких и средних скоростях, когда динамические нагрузки от неточности изготовления невелики, в планетарных, открытых передачах, а также при необходимости осевого перемещения колёс.
Косозубые колёса (более 30%) имеют большую плавность хода и применяются для ответственных механизмов при средних и высоких скоростях.
Шевронные колёса имеют достоинства косозубых колёс плюс уравновешенные осевые силы и используются в высоконагруженных передачах.
Конические передачи применяют только в тех случаях, когда это необходимо по условиям компоновки машины; винтовые - лишь в специальных случаях.
Колёса внутреннего зацепления вращаются в одинаковых направлениях и применяются обычно в планетарных передачах.
Для изготовления зубчатых колес применяют следующие материалы :
Сталь углеродистую обыкновенного качества марок Ст5, Ст6; качественную сталь марок 35, 40, 45, 50, 55; легированную сталь марок 12ХНЗА, 30ХГС, 40Х, 35Х, 40ХН, 50Г; сталь 35Л, 45Л, 55Л;
Серый чугун марок СЧ10, СЧ15, СЧ20, СЧ25, СЧ30, СЧ40, высококачественный чугун марок ВЧ50-2, ВЧ45-5;
Неметаллические материалы (текстолит марок ПТК, ПТ, ПТ-1, лигнофоль, бакелит, капрон и др.).
Практикой эксплуатации и специальными исследованиями установлено, что нагрузка, допускаемая по контактной прочности зубьев, определяется в основном твердостью материала. Высокую твердость в сочетании с другими характеристиками, а, следовательно, малые габариты и массу передачи можно получить при изготовлении зубчатых колес из сталей, подвергнутых термообработке. Сталь в настоящее время - основной материал для изготовления зубчатых колес и в особенности для зубчатых колес высоконагруженных передач.
Важнейшими критериями работоспособности зубчатых колёс приводов являются объёмная прочность зубьев и износостойкость их активных поверхностей. Нагрузочная способность хорошо смазанных поверхностей ограничивается сопротивлением выкрашиванию. Для уменьшения расхода материалов назначают высокую твёрдость трущихся поверхностей.
Несущая способность зубчатых передач по контактной прочности тем выше, чем выше поверхностная твердость зубьев. Повышение твердости в два раза позволяет уменьшить массу редуктора примерно в четыре раза.
В зависимости от твердости (или термообработки ) стальные зубчатые, колеса разделяют на две основные группы: твердостью Н 350 НВ - с объемной закалкой, закалкой ТВЧ, цементацией, азотированием и др. Эти группы различны по технологии, нагрузочной способности и способности к приработке.
Объемная закалка - наиболее простой способ получения высокой твердости зубьев. При этом зуб становится твердым по всему объему. Для объемной закалки используют углеродистые и легированные стали со средним содержанием углерода 0,35...0,5% (стали 45, 40Х, 40ХН и т. д.). Твердость на поверхности зуба 45...55 HRC.
Недостатки объемной закалки : коробление зубьев и необходимость последующих отделочных операций, понижение изгибной прочности при ударных нагрузках (материал приобретает хрупкость); ограничение размеров заготовок, которые могут воспринимать объемную закалку. Последнее связано с тем, что для получения необходимой твердости при закалке скорость охлаждения не должна быть ниже критической. С увеличением размеров сечений детали скорость охлаждения падает, и если ее значение будет меньше критической, то получается так называемая мягкая закалка. Мягкая закалка дает пониженную твердость.
Объемную закалку во многих случаях заменяют поверхностными термическими и химико-термическими видами обработки, которые обеспечивают высокую поверхностную твердость (высокую контактную прочность) при сохранении вязкой сердцевины зуба (высокой изгибной прочности при ударных нагрузках).
Поверхностная закалка токами высокой частоты или пламенем ацетиленовой горелки обеспечивает Н = (48...54) HRC и применима для сравнительно крупных зубьев (m > 5 мм). При малых модулях опасно прокаливание зуба насквозь, что делает зуб хрупким и сопровождается его короблением. При относительно тонком поверхностном закаливании зуб искажается мало. И все же без дополнительных отделочных операций трудно обеспечить степень точности выше 8-й. Закалка ТВЧ требует специального оборудования и строгого соблюдения режимов обработки. Стоимость обработки ТВЧ значительно возрастает с увеличением размеров колес. Для поверхностной закалки используют стали 40Х, 40ХН, 45 и др.
Цементация (насыщение углеродом поверхностного слоя с последующей закалкой) - длительный и дорогой процесс. Однако она обеспечивает очень высокую твердость (58....63HRC). При закалке после цементации форма зуба искажается, а поэтому требуются отделочные операции. Для цементации применяют низкоуглеродистые стали простые (сталь 15 и 20) и легированные (20Х, 12ХНЗА и др.). Легированные стали обеспечивают повышенную прочность сердцевины и этим предохраняют продавливание хрупкого поверхностного слоя при перегрузках. Глубина цементации около 0,1 ...0,15 от толщины зуба, но не более 1,5...2 мм. При цементации хорошо сочетаются весьма высокие контактная и изгибная прочности. Ее применяют в изделиях, где масса и габариты имеют решающее значение (транспорт, авиация и т. п.).
Нитроцементация - насыщение углеродом в газовой среде. При этом по сравнению с цементацией сокращаются длительность и стоимость процесса,- упрочняется тонкий поверхностный слой (0,3...0,8 мм) до 60...63 HRC, коробление уменьшается, что позволяет избавиться от последующего шлифования. Нитроцементация удобна в массовом производстве и получила широкое применение в редукторах общего назначения, в автомобилестроении и других отраслях - материалы 25ХГМ, 25ХГТ и др.
Азотирование (насыщение поверхностного слоя азотом) обеспечивает не меньшую твердость, чем при цементации.
Основные элементы зубчатой передачи. Термины, определения и обозначения
Одноступенчатая зубчатая передача состоит из двух зубчатых колес - ведущего и ведомого. Меньшее по числу зубьев из пары колес называют шестерней, а большее колесом. Термин «зубчатое колесо» является общим. Параметрам шестерни (ведущего колеса) приписывают при обозначении нечетные индексы (1, 3, 5 и т. д.), а параметрам ведомого колеса - четные (2, 4, 6 и т. д.).
Зубчатое зацепление характеризуется следующими основными параметрами:
da - диаметр вершин зубьев; dr - диаметр впадин зубьев;
da - начальный диаметр; d - делительный диаметр;
рt - окружной шаг; h - высота зуба;
ha - высота ножки зуба; с - радиальный зазор;
b - ширина венца (длина зуба); еt - окружная ширина впадины зуба;
st - окружная толщина зуба; аw - межосевое расстояние;
а - делительное межосевое расстояние; Z - число зубьев.
Делительная окружность - окружность, по которой обкатывается инструмент при нарезании. Делительная окружность связана с колесом и делит зуб на головку и ножку.
Лекция 12. Назначение. Классификация. Зубчатые передачи.
Раздел 6 Механические передачи.
1. Где применяют подшипники? Что представляет собой подшипник скольжения? Какие подшипники скольжения (по конструкции) вы знаете?
2. Какой материал используют для изготовления подшипников скольжения? Назовите режимы трения при работе подшипников скольжения.
3. Как рассчитывают подшипники скольжения?
4. Как устроен подшипник качения? Какие существуют разновидности
подшипников качения?
5. Какие вы знаете типы подшипников качения?
6. Как обозначают подшипники качения?
7. Как проводится расчет подшипников качения?
Большинство современных машин и установок состоят из неподвижной части – статора и подвижной – ротора. Чтобы подвижной части машины или аппарата (шпиндель, вал с мешалкой и т.д.) передать энергию и движение, необходимы специальные устройства, в качестве которых применяют двигатели и передачи, образующие привод. Функция передачи движения в большинстве случаев совмещается с преобразованием его параметров и соответствующим изменением действующих усилий, моментов, а иногда и с преобразованием самого вида движения (вращательного в поступательное или др.). Передачи являются важным элементом приводов машин. Наибольшее распространение получили механические передачи. Они используются преимущественно для передачи наиболее распространенного в машинах вращательного движения и реже – для преобразования вращательного движения в поступательное или наоборот.
Механические передачи различаются по принципу действия: на фрикционные , действующие за счет сил трения, создаваемых между элементами передачи (ременные, фрикционные) и передачи зацеплением (зубчатые, червячные, винтовые).
По характеру изменения скорости передачи бывают: понижающие (редукторы) и повышающие (мультипликаторы), соответственно уменьшающие или увеличивающие скорость вращения ведомого (выходного) вала по сравнению со скоростью ведущего (входного) вала передачи. При этом в зависимости от назначения и устройства передачи отношение угловых скоростей может быть постоянным или переменным (регулируемым). В последнем случае возможно ступенчатое или бесступенчатое регулирование в определенных пределах.
По взаимному расположению валов в пространстве передача движения осуществляется между параллельными, пересекающимися или перекрещивающимися валами.
По конструктивному оформлению передачи бывают – открытые, не имеющие общего, закрывающего их корпуса и закрытые, заключенные в общий корпус.
Основными кинематическими характеристиками передач вращения являются угловые скорости , или числа оборотов в единицу времени, совместно работающих валов и их отношение, именуемое передаточным отношением
Энергетическими характеристиками механических передач являются передаваемая мощность P кВт и коэффициент полезного действия (к.п.д.) h – отношение мощности сил полезных сопротивлений к мощности движущих сил
Так как мощность и момент на любом валу связаны зависимостями
кВт или кГм,
запишем соотношения между моментами на ведущем Т 1 и ведомом Т 2 валах
Для многоступенчатых передач, составленных из нескольких одноступенчатых, справедливы зависимости
; .
Механические передачи обладают многими достоинствами, обеспечивающими их широкое использование в современном машиностроении. Они компактны, отличаются высокой надежностью в эксплуатации, позволяют относительно просто осуществлять необходимые преобразования параметров и видов движения, имеют высокий к.п.д.
Зубчатые передачи. Зубчатые передачи являются разновидностью механических передач, работающих на принципе зацепления. Их применяют для передачи вращательного движения между валами с параллельными, пересекающимися и перекрещивающимися осями, а также для преобразования вращательного движения в поступательное и наоборот.
Передача вращательного движения между параллельными валами осуществляется цилиндрическими колесами с прямыми (рис.6.1а ), косыми (рис.6.1б ) и шевронными (рис.6.1в ) зубьями. Различают передачи внешнего (рис.6.1а-в ) и внутреннего зацепления (рис.6.1г ).
Преобразование вращательного движения в поступательное и наоборот осуществляется цилиндрическим колесом и рейкой (рис.6.1д ). Передачи между валами с пересекающимися осями осуществляются коническими колесами с прямыми (рис.6.1е )., круговыми (рис.6.1ж ). и тангенциальными (рис.6.1з ) зубьями.
Между перекрещивающимися валами вращение передается с помощью зубчато – винтовых передач.
Зубчатые передачи составляют наиболее распространенную группу передач благодаря таким достоинствам, как малые габариты, высокий к.п.д., постоянство передаточного отношения, возможность применения в широком диапазоне скоростей и передаточных отношений, надежность в работе.
Геометрия и кинематика эвольвентного зацепления . Зубчатые передачи в преобладающем большинстве изготавливают с эвольвентным профилем зубьев. Это объясняется тем, что эвольвентное зацепление имеет ряд существенных достоинств: простое изготовление и постоянство передаточного отношения, малые скорости скольжения и долговечность колес.
Эвольвентой
(рис.6.2) называют кривую, описываемую точкой С
прямой АВ
, перекатывающейся без скольжения по окружности диаметра d b
, которую называют основной окружностью.
Для таких передач общая нормаль NN к взаимодействующим профилям (рис.6.3), в любой момент движения сопряженных зубьев должна проходить через точку П – полюс зацепления, лежащий на линиицентров и делящий межосевое расстояние на отрезки, обратно пропорциональные передаточному отношению , где d ω2 и d ω1 – диаметры воображаемых окружностей, касающихся друг друга в полюсе зацепления П и перекатывающихся при вращении одна по другой без скольжения. Эти окружности называются начальными окружностями. Прямая NN называется линией зацепления , т.к. она является траекторией точек контакта сопряженных зубьев при вращении колес. Угол α ω между линией зацепления и прямой, перпендикулярной межосевой линии О 1 О 2 называется углом зацепления.
Вершины и впадины зубьев очерчиваются соответственно окружностями выступов с диаметрами, и впадин – , .
В качестве исходного контура для эвольвентного зацепления принят контур, расположенный на прямой – рейка (рис.6.4). Линия а-а,
на которой толщина зуба равна ширине впадины, называется средней линией рейки.
Расстояние р между соответственными точками профилей соседних зубьев, измеренное вдоль средней линии, называется шагом зацепления , а отношение – модулем зацепления.
Применительно к зубчатому колесу окружность, на которой шаг равен шагу исходного контура р , называется делительной окружностью d. Очевидно, что, где z – число зубьев колеса. Откуда. Соответственно, окружной модуль представляет собой частное от деления диаметра делительной окружности на число зубьев колеса. Часть зуба, расположенная между окружностями выступов и делительной, называется головкой зуба h a , а между окружностью впадин и делительной – ножкой зуба h f .
Цилиндр, диаметр которого равен диаметру делительной окружности, называется делительным цилиндром. Кратчайшее расстояние по делительному цилиндру между одноименными профильными поверхностями двух смежных зубьев называется нормальным шагом р n (рис.6.5). Справедлива зависимость, где b – угол наклона линии зуба. Нормальный модуль вычисляется по формуле. Для прямозубых передач (b = 0) окружные и нормальные шаги и модули соответственно совпадают. Величины модулей определяются стандартом. Для косозубых цилиндрических колес стандартными являются нормальные модули.
Для цилиндрических зубчатых передачдолжны выполняться следующие соотношения:
Межосевое расстояние
Силы, действующие в цилиндрических передачах (рис.6.6). Нормальную силу F n , давления одного зуба на другой, возникающую при работе сопряженных зубьев можно разложить на и, а, в свою очередь, на и.
В результате имеем
,
где F t – окружная сила, Т – вращающий момент, d – делительный диаметр.
Из схемы сил
,
где F r – радиальная, а F a – осевая силы, – угол зацепления, – угол наклона линии зуба.
Нормальная к поверхности зуба сила .
Расчет зубьев цилиндрических передач
и расчет на контактную прочность
в большинстве случаев является основой для определения габаритных размеров передачи. Исходной зависимостью для расчета контактных напряжений
(рис.6.7), возникающих на рабочих поверхностях зубьев служит формула Герца-Беляева
,
где Z Е – коэффициент, учитывающий механические свойства контактирующих материалов; q – нормальная нагрузка на единицу длины контактной линии; – приведенный радиус кривизны контактирующих поверхностей, R 1 и R 2 – радиусы кривизны профилей контактирующих зубьев.
Подставляя в эту формулу параметры и характеристики цилиндрических зубчатых передач с эвольвентным профилем зубьев, после ряда преобразований получим формулу для расчета контактной прочности рабочих поверхностей зубьев
,
где Z Е – коэффициент, учитывающий механические свойства материалов шестерни и колеса; Z e – коэффициент, учитывающий суммарную длину контактных линий; Z Н – коэффициент, учитывающий форму сопряженных поверхностей зубьев; К Н – к оэффициент нагрузки (учитывает динамическую нагрузку и неравномерность распределения нагрузки по ширине зуба и между зубьями); F t – окружная сила на делительном диаметре d 1 ; b – ширина венца колеса; u – передаточное число.
Подавляющее большинство механических передач имеет в своей основе зубчатые зацепления. Другими словами, в зубчатой передаче усилие передается благодаря зацеплению пары зубчатых колес (зубчатой пары). Зубчатые передачи активно используются, позволяя изменять скорость вращения, направление, моменты.
Основной задачей является преобразования вращательного движения, а также изменение расположения элементов и ряд других функций, которые необходимы для работы узлов, агрегатов и механизмов. Далее мы рассмотрим типы зубчатых передач, их особенности, а также достоинства зубчатых передач и их недостатки.
Читайте в этой статье
Как уже было сказано, зубчатые зацепления (передачи зацеплением) позволяют эффективно реализовать передачу вращательного движения, которое поступает от двигателя.
Параллельно осуществляется преобразование движения, изменяется частота вращения, величина , направление осей вращения и т.д. Чтобы выполнять такие задачи, существуют разные виды передач. Прежде всего, их принято классифицировать согласно особенностям расположения осей вращения.
- Цилиндрическая передача. Такая передача состоит из пары, которая обычно имеет разное количество зубьев, а оси зубчатых колес цилиндрической передачи являются параллельными. Также отношение чисел зубьев принято называть передаточным отношением. Меньшее по размеру зубчатое колесо называется шестерней, тогда как большое называют зубчатым колесом.
В том случае, когда шестерня ведущая, при этом передаточное число оказывается больше единицы, такая передача является понижающей, так как зубчатое колесо будет вращаться с меньшей частотой, чем шестерня. Также одновременно при условии уменьшения угловой скорости происходит увеличение крутящего момента на валу. В случае, когда передаточное число оказывается меньше единицы, такая передача буде повышающей.
- Коническое зацепление. Особенностью является то, что оси зубчатых колес будут пересекаться, вращение передается между валами, расположенными под тем или иным углом. Передача будет понижающей или повышающей с учетом того, какое из колес оказывается ведущим в передаче данного типа.
- Червячная передача. Такая передача отличается тем, что имеет оси вращения, которые скрещиваются. Большое передаточное число получается в результате соотношения числа зубьев колеса, а также числа заходов червяка. Сами червяки бывают однозаходными, двухзаходными или четырехзаходными. Также важной особенностью червячной передачи считается то, что в этом случае вращение передается исключительно от червяка на червячное колесо. При этом обратный процесс является нереализуемым по причине ильного трения. Данная система имеет способность самостоятельно затормаживаться благодаря применению червячных редукторов (например, в механизмах для подъема грузов).
- Реечное зацепление, которое удается реализовать при помощи зубчатого колеса и рейки. Такое решение позволяет эффективно преобразовать вращательное движение в поступательное и обратно. Например, в автомобиле решение обычно используется в устройстве рулевого управления (рулевая рейка).
- Винтовые передачи. Такие передачи используются в том случае, если валы скрещиваются. При этом контакт зубьев зацепления точечный, сами зубья сильно изнашиваются под нагрузками. Передачи данного типа зачастую используются в разных приборах.
- Планетарная передача (). Данный тип зацепления отличается от остальных тем, что в нем использованы зубчатые колеса, имеющие подвижные оси. Как правило, присутствует жестко закрепленное наружное колесо, которое имеет внутреннюю резьбу.
Еще имеется центральное колесо, а также водило с сателлитами. Указанные элементы перемещаются по окружности неподвижного колеса, благодаря чему они вращают центральное колесо. В этом случае происходит передача вращения от водила на центральное колесо или же обратно.
Зубчатые передачи могут иметь наружное или внутреннее зацепление. Если с наружным все понятно (в данном случае схема зубчатой передачи предполагает, что зубья расположены сверху), то при внутреннем зацеплении зубья большего колеса располагаются на внутренней поверхности. Также вращение возможно только в одном направлении.
Рассмотрев выше основные виды зацеплений (зубчатых передач), следует добавить, что при этом указанные типы могут использоваться в разных сочетаниях с учетом особенностей тех или иных кинематических схем.
- Еще зубчатые передачи могут отличаться по форме зубьев, профилю и типу. С учетом отличий принято выделять следующие зацепления: эвольвентные, круговые и циклоидальные. При этом чаще всего используются именно эвольвентные зацепления, так как технологически данное решение превосходит другие аналоги.
Прежде всего, такие зубья нарезаются при помощи простого реечного инструмента. Указанное зацепление имеет постоянное передаточное отношение, которое никак не зависит от степени смещения межцентрового расстояния. Недостатком зацепления является только то, что во время передачи большой мощности сказывается небольшое пятно контакта в двух выпуклых поверхностях зубьев. Результат — разрушение поверхности и другие дефекты материала.
Еще добавим, что круговое зацепление отличается тем, что выпуклые зубья шестерни сцеплены с вогнутыми колесами. Это позволяет значительно увеличить пятно контакта, однако также сильно возрастает сила трения в указанных парах.
- Также можно отдельно выделить сами виды зубчатых колес: прямозубые, косозубые, шевронные и криволинейные. Прямозубые являются наиболее распространенными типами пар, они просты в разработке, дешевы в изготовлении и надежны в рамках эксплуатации. Линия контакта в данном случае параллельна оси вала. Такие колеса отличаются дешевизной производства, однако способны передать сравнительно небольшой максимальный крутящий момент по сравнению с косозубыми и шевронными зубчатыми колесами.
Косозубые колеса оптимально применять в том случае, если частота вращения очень высокая. Данное решение позволяет добиться плавности и снижения шума. Минусом принято считать большую нагрузку на подшипники, так как возникают осевые усилия.
Шевронные колеса имеют ряд преимуществ, свойственных косозубым парам. Прежде всего, они не создают дополнительной нагрузки на подшипники осевыми усилиями (силы разнонаправлены).
Криволинейные колеса обычно используют в том случае, когда необходимы максимальные передаточные отношения. Такие колеса создают меньше шума при работе, а также более эффективно работают на изгиб.
Из чего изготавливаются зубчатые колеса и шестерни
Как правило, в основе зубчатого колеса лежит сталь. При этом шестерня должна иметь большую прочность, так как сами колеса могут иметь разные характеристики по прочности.
По этой причине шестерни изготавливаются из разных материалов, а также такие изделия проходят дополнительную термическую обработку и/или комплексную химическую и температурную обработку.
Например, шестерни, которые выполнены из легированной стали, также проходят процесс упрочнения поверхности, в рамках которого может быть использован метод, позволяющий добиться желаемых характеристик (азотирование, цементация или цианирование). Если для изготовления шестерни используется углеродистая сталь, такой материал проходит поверхностную закалку.
Что касается зубьев, для них предельно важна прочность поверхности, а также сердцевина должна быть мягкой и вязкой. Данные характеристики позволяют избежать излома и быстрого износа рабочей нагруженной поверхности. Еще добавим, что колесные пары механизмов, где нет больших нагрузок и высокой частоты вращения, изготавливают из чугуна. Также можно встретить в качестве материала для изготовления колесных пар бронзу, латунь и даже всевозможные виды пластика.
Сами зубчатые колеса выполняются из заготовки, полученной методом литья или штамповки. Затем применяется метод нарезки зубьев. Нарезка осуществляется путем использования методов копирования, обкатки. Метод обкатки дает возможность изготовить зубья разной конфигурации при помощи одного инструмента (долбяк, червячные фрезы, рейка).
Чтобы осуществить нарезку методом копирования, требуются пальцевые фрезы. После нарезки выполняется термическая обработка. Если же нужно зацепление высокой точности, после такой термообработки дополнительно выполняется шлифовка и обкатка.
Прежде всего, среди достоинств зубчатой передачи можно выделить:
Также выделяют и недостатки зубчатой передачи:
- повышенные требования к качеству изготовления и точности установки;
- при высокой скорости вращения возникает шум по причине возможных неточностей при изготовлении шага и профиля зубьев;
- повышенная жесткость не позволяет эффективно компенсировать динамические нагрузки, в результате чего возникает разрушение и пробуксовки, появляются дефекты;
Напоследок отметим, что во время обслуживания механизм нужно осматривать, производя проверку состояния зубчатых колес, шестерен и зубьев на предмет повреждений, трещин, сколов и т.д.
Также проверяется само зацепление и его качество (часто используется краска, которая наносится на зубья). Нанесение краски позволяет изучить величину пятна контакта, а также расположение относительно высоты зуба. Для регулировки зацепления применяются прокладки, которые ставятся в подшипниковые узлы.
Подведем итоги
Как видно, зубчатая передача является достаточно распространенным решением, которое используется в различных узлах, агрегатах и механизмах. С учетом того, что существует несколько типов таких передач, перед использованием одного или другого вида, в рамках проектирования конструкторы учитывают кинематические и силовые характеристики работы разных механизмов и агрегатов.
С учетом ряда особенностей и нагрузок подбирается вид зубчатой передачи, ее габариты, определяется степень нагрузки. После этого выполняется подбор материалов для изготовления зубчатых пар, а также способы необходимой обработки и нарезки зубьев. При расчетах отдельно учитывается модуль зацепления, величины смещений, количество зубьев шестерни и колеса, расстояние между осями, ширина венцов и т.д.
При этом основными условиями, которые определяют срок службы зубчатой передачи и ее ресурс, принято считать общую износостойкость поверхностей зубьев, а также прочность зубьев на изгиб. Чтобы получить нужные характеристики, в рамках проектирования производства зубчатых механизмов указанным особенностям уделяется отдельное повышенное внимание.
Читайте также
Гипоидная передача в устройстве трансмиссии автомобиля: что такое гипоидная передача, в чем ее особенности и отличия, а также преимущества и недостатки.
Зубчатые передачи. Общие сведения
Зубчатой передачей называется трехзвенный механизм, в котором два подвижных зубчатых звена образуют с неподвижным звеном вращательную или поступательную пару. Зубчатое звено передачи может представлять собой колесо, сектор или рейку. Зубчатые передачи служат для преобразования вращательных движений или вращательного движения в поступательное.
Все применяемые здесь и в дальнейшем термины, определения и обозначения, относящиеся к зубчатым передачам, соответствуют ГОСТ 16530-83 «Передачи зубчатые», ГОСТ 16531-83 «Передачи зубчатые цилиндрические» и ГОСТ 19325-73 «Передачи зубчатые конические».
Зубчатое зацепление представляет собой высшую кинематическую пару, так как зубья теоретически соприкасаются между собой по линиям или точкам, причем меньшее зубчатое колесо пары называется шестерней, а большее-колесом. Сектор цилиндрического зубчатого колеса бесконечно большого диаметра называется зубчатой рейкой.
Зубчатые передачи можно классифицировать по многим признакам, а именно: по расположению осей валов (с параллельными, пересекающимися, скрещивающимися осями и соосные); по условиям работы (закрытые - работающие в масляной ванне и открытые-работающие всухую или смазываемые периодически); по числу ступеней (одноступенчатые, многоступенчатые); по взаимному расположению колес (с внешним и внутренним зацеплением); по изменению частоты вращения валов (понижающие, повышающие); по форме поверхности, на которой нарезаны зубья (цилиндрические, конические); по окружной скорости колес (тихоходные при скорости до 3 м/с, среднескоростные при скорости до 15 м/с, быстроходные при скорости выше 15 м/с); по расположению зубьев относительно образующей колеса (прямозубые, косозубые, шевронные, с криволинейными зубьями); по форме профиля зуба (эвольвентные, круговые, циклоидальные).
Кроме перечисленных существуют передачи с гибкими зубчатыми колесами, называемые волновыми.
Основные виды зубчатых передач (рис.) с параллельными осями: а - цилиндрическая прямозубая, б- цилиндрическая косозубая, в- шевронная, г - с внутренним зацеплением; с пересекающимися осями: д- коническая прямозубая, е - коническая с тангенциальными зубьями, ж - коническая с криволинейными зубьями; со скрещивающимися осями: з- гипоидная, и- винтовая; к - зубчато-реечная прямозубая (гипоидная и винтовая передачи относятся к категории гиперболоидных передач).
Зубчатая передача, оси которой расположены под углом 90°, называется ортогональной.
Достоинство зубчатых передач заключается прежде всего в том, что при одинаковых характеристиках они значительно более компактны, по сравнению с другими видами передач. Кроме того, зубчатые передачи имеют более высокий к. п. д.(до 0,99 в одной ступени), сохраняют постоянство передаточного числа, создают относительно небольшую нагрузку на опоры валов, имеют большую долговечность и надежность работы в широких диапазонах мощностей (до десятков тысяч киловатт), окружных скоростей (до 150 м/с) и передаточных чисел (до нескольких сотен).
Недостатки зубчатых передач: сложность изготовления точных передач, возможность возникновения шума и вибраций при недостаточной точности изготовления и сборки, невозможность бесступенчатого регулирования частоты вращения ведомого вала.
Зубчатые передачи являются наиболее распространенными типами механических передач и находят широкое применение во всех отраслях машиностроения, в частности в металлорежущих станках, автомобилях, тракторах, сельхозмашинах и т. д.; в приборостроении, часовой промышленности и др. Годовое производство зубчатых колес в нашей стране исчисляется сотнями миллионов штук, а габаритные размеры их от долей миллиметра до десяти и более метров. Такое широкое распространение зубчатых передач делает необходимой большую научно-исследовательскую работу по вопросам конструирования и технологии изготовления зубчатых колес и всестороннюю стандартизацию в этой области. В настоящее время стандартизованы термины, определения, обозначения, элементы зубчатых колес и зацеплений, основные параметры передач, расчет геометрии, расчет цилиндрических эвольвентных передач на прочность, инструмент для нарезания зубьев и многое другое.
Основная кинематическая характеристика всякой зубчатой передачи - передаточное число, определяемое по стандарту как отношение числа зубьев колеса к числу зубьев шестерни и обозначаемое и, следовательно,
Определение передаточного отношения остается таким же, как для других механических передач, т. е.
Потери энергии в зубчатых передачах зависят от типа передачи, точности ее изготовления, смазки и складываются из потерь на трение в зацеплении, в опорах валов и (для закрытых передач) потерь на перемешивание и разбрызгивание масла. Потерянная механическая энергия переходит в тепловую, что в некоторых случаях делает необходимым тепловой расчет передачи.
Потери в зацеплении характеризуются коэффициентом , потери в одной паре подшипников - коэффициентом и потери на перемешивание и разбрызгивание масла - коэффициентом . Общий к. п. д. одноступенчатой закрытой передачи
Ориентировочно = 0,96...0,98 (закрытые передачи), = 0,95...0,96 (открытые передачи), = 0,99...0,995 (подшипники качения), = 0,96...0,98 (подшипники скольжения), = 0,98...0,99.
Поверхности взаимодействующих зубьев колес, обеспечивающие заданное передаточное отношение, называются сопряженными. Процесс передачи движения в кинематической паре, образованной зубчатыми колесами, называется зубчатым зацеплением.
Цилиндрическая прямозубая передача
На рис. изображено цилиндрическое колесо с прямыми зубьями. Часть зубчатого колеса, содержащая все зубья, называется венцом; часть колеса, насаживаемая на вал, называется ступицей. Делительная окружность диаметром d делит зуб на две части - головку зуба высотой h a и ножку зуба высотой h f , высота зуба h = h а + h f . Расстояние между одноименными профилями соседних зубьев, измеренное по дуге делительной окружности, называется окружным делительным шагом зубьев и обозначается р. Шаг зубьев слагается из окружной толщины зуба s и ширины впадины е. Длина хорды, соответствующая окружной толщине зуба, называется толщиной по хорде и обозначается . Линейная величина, в раз меньшая окружного шага, называется окружным делительным модулем зубьев, обозначается т и измеряется в миллиметрах (впредь слова «окружной делительный» в терминах будем опускать)
Модуль зубьев - основной параметр зубчатого колеса. Для пары колес, находящихся в зацеплении, модуль должен быть одинаковым. Модули зубьев для цилиндрических и конических передач регламентированы ГОСТ 9563-60*. Значения стандартных модулей от 1 до 14 мм приведены в табл.
Модули, мм
1-й ряд 1; 1,25; 1,5; 2; 2,5; 3; 4; 5; 6; 8; 10; 12
2-й ряд 1,125; 1,375; 1,75; 2,25; 2,75; 3,5; 4,5; 5,5; 7; 9; 11; 14
Примечание . При назначении модулей 1-й ряд следует предпочитать 2-му.
Все основные параметры зубчатых колес выражают через модули, а именно: шаг зубьев
диаметр делительной окружности
Последняя формула позволяет определить модуль как число миллиметров диаметра делительной окружности, приходящихся на один зуб колеса.
В соответствии со стандартным исходным контуром для цилиндрических зубчатых колес высота головки зуба h a = т, высота ножки зуба h f = 1,25т. Высота зубьев цилиндрических колес
h = h а + h f = 2,25m .
Диаметр вершин зубьев
d a = m (z + 2),
диаметр впадин
d f = m (z – 2,5).
Расстояние между торцами зубьев колеса называется шириной венца. Контакт пары зубьев цилиндрической прямозубой передачи теоретически происходит по линии, параллельной оси; длина линии контакта равна ширине венца. В процессе работы передачи пара зубьев входит в зацепление сразу по всей длине линии контакта (что сопровождается ударом зубьев), после чего эта линия перемещается по высоте зуба, оставаясь параллельной оси.
Межосевое расстояние цилиндрической передачи с внешним и внутренним зацеплением
называется делительным межосевым расстоянием (знак минус для внутреннего зацепления). Если межосевое расстояние отличается от делительного, то оно обозначается а w .
ГОСТ 1643-81 на допуски для цилиндрических зубчатых колес и передач установлены двенадцать степеней точности, обозначенных цифрами (первая степень - наивысшая). Для каждой степени точности установлены нормы: кинематической точности, плавности работы и контакта зубьев колес и передач.
В процессе изготовления зубчатых передач неизбежны погрешности в шаге, толщине и профиле зубьев, неизбежно радиальное биение венца, колебание межосевого расстояния при беззазорном зацеплении контролируемого и измерительного колес и т. д. Все это создает кинематическую погрешность в углах поворота ведомого колеса, выражаемую линейной величиной, измеряемой по дуге делительной окружности. Кинематическая погрешность определяется как разность между действительным и расчетным углом поворота ведомого колеса. Нормы кинематической точности регламентируют допуски на кинематическую погрешность и ее составляющие за полный оборот колеса. Нормы плавности устанавливают допуски на циклическую (многократно повторяющуюся за один оборот) кинематическую погрешность колеса и ее составляющие. Нормы контакта устанавливают размеры суммарного пятна контакта зубьев передачи (в процентах от размеров зубьев) и допуски на параметры, влияющие на этот контакт.
В машиностроении зубчатые передачи общего назначения изготовляют по 6-9-й степеням точности. Цилиндрические прямозубые колеса 6-й степени точности применяют при окружных скоростях колес до 15 м/с; 1-й степени-до 10 м/с; 8-й степени - до 6 м/с; 9-й - до 2 м/с.
Рассмотрим силы, действующие в зацеплении прямозубой цилиндрической передачи. При изображенном на этом рисунке контакте пары зубьев в полюсе П скольжение (следовательно, и трение) отсутствует, зацепление будет однопарным и силовое взаимодействие колес будет заключаться в передаче по линии давления (нормали NN ) силы нормального давления . Разложим эту силу на две взаимно перпендикулярные составляющие и , называемые соответственно окружным и радиальным усилиями, тогда
, ,
где - угол зацепления.
Если известен передаваемый вращающий момент Т и диаметр d делительной окружности, то
(так как = 20°, то ).
Сила , вызывает вращение ведомого колеса и изгибает вал колеса в горизонтальной плоскости, сила г изгибает вал в вертикальной плоскости.
Цилиндрические передачи с косыми и шевронными зубьями
Косозубыми называют колеса, у которых теоретическая делительная линия зуба является частью винтовой линии постоянного шага (теоретической делительной линией называется линия пересечения боковой поверхности зуба с делительной цилиндрической поверхностью). Линия зуба косозубых колес может иметь правое и левое направление винтовой линии. Угол наклона линии зуба обозначается .
Косозубая передача с параллельными осями имеет противоположное направление зубьев ведущего и ведомого колес и относится к категории цилиндрических зубчатых передач, так как начальные поверхности таких зубчатых колес представляют собой боковую поверхность цилиндров. Передача с косозубыми колесами, оси которых скрещиваются, имеет одинаковое направление зубьев обоих колес и называется винтовой зубчатой передачей, которая относится к категории гиперболоидных зубчатых передач, так как начальные поверхности таких зубчатых колес являются частями однополостного гиперболоида вращения; делительные поверхности этих колес - цилиндрические.
У косозубых передач контактные линии расположены наклонно по отношению к линии зуба, поэтому в отличие от прямых косые зубья входят в зацепление не сразу по всей длине, а постепенно, что обеспечивает плавность зацепления и значительное снижение динамических нагрузок и шума при работе передачи. Поэтому косозубые передачи по сравнению с прямозубыми допускают значительно большие предельные окружные скорости колес. Так, например, косозубые колеса 6-й степени точности применяют при окружной скорости до 30 м/с; 7-й степени-до 15 м/с; 8-й степени - до 10 м/с; 9-й - до 4 м/с.
Силу нормального давления в зацеплении косозубых колес можно разложить на три взаимно перпендикулярные составляющие (рис. 7.10,б): окружную силу , радиальную силу и осевую силу , равные:
где Т- передаваемый вращающий момент; - угол зацепления.
Наличие осевой силы - существенный недостаток косозубых передач. Во избежание больших осевых сил в косозубой передаче угол наклона линии зуба ограничивают значениями =8...20°, несмотря на то, что с увеличением увеличивается прочность зубьев, плавность работы передачи, ее нагрузочная способность.
В современных передачах косозубые колеса имеют преимущественное распространение.
Цилиндрическое зубчатое колесо, венец которого по ширине состоит из участков с правыми и левыми зубьями, называется шевронным. Часть венца с зубьями одинакового направления называется полушевроном. Из технологических соображений шевронные колеса изготовляют двух типов: с дорожкой посредине колеса (а) и без дорожки (б). В шевронном колесе осевые силы на полушевронах, направленные в противоположные стороны, взаимно уравновешиваются внутри колеса и на валы и опоры валов не передаются. Поэтому у шевронных колес угол наклона зубьев принимают в пределах = 25...40°, в результате чего повышается прочность зубьев, плавность работы передачи и ее нагрузочная способность. Поэтому шевронные колеса применяют в мощных быстроходных закрытых передачах. Недостатком шевронных колес является высокая трудоемкость и себестоимость изготовления.
Геометрические, кинематические и прочностные расчеты шевронной и косозубой передач аналогичны.
Материалы цилиндрических колес
Материалы для изготовления зубчатых колес в машиностроении- стали, чугуны и пластмассы; в приборостроении зубчатые колеса изготовляют также из латуни, алюминиевых сплавов и др. Выбор материала определяется назначением передачи, условиями ее работы, габаритами колес и даже типом производства (единичное, серийное или массовое) и технологическими соображениями.
Общая современная тенденция в машиностроении - стремление к снижению материалоемкости конструкций, увеличению мощности, быстроходности и долговечности машины. Эти требования приводят к необходимости уменьшения массы, габаритов и повышения нагрузочной способности силовых зубчатых передач. Поэтому основные материалы для изготовления зубчатых колес - термообработанные углеродистые и легированные стали, обеспечивающие высокую объемную прочность зубьев, а также высокую твердость и износостойкость их активных поверхностей.
Критерии работоспособности зубчатых колес и
Под действием сил нормального давления и трения зуб колеса испытывает сложное напряженное состояние, но решающее влияние на его работоспособность оказывают два фактора: контактные напряжения и напряжения изгиба , которые действуют на зуб только во время нахождения его в зацеплении и являются, таким образом, повторно-переменными.
Повторно-переменные напряжения изгиба вызывают появление усталостных трещин у растянутых волокон основания зуба (место концентрации напряжений), которые с течением времени приводят к его поломке (рис. а, б).
Повторно-переменные контактные напряжения и силы трения приводят к усталостному изнашиванию активных поверхностей зубьев. Так как сопротивление усталостному изнашиванию у опережающих поверхностей выше, чем у отстающих, то нагрузочная способность головок зубьев выше, чем ножек. Этим объясняется отслаивание и выкрашивание частиц материала на активной поверхности ножек зубьев (рис. в ) при отсутствии видимых усталостных повреждений головок. Усталостное изнашивание активных поверхностей зубьев характерно для работы закрытых передач.
В открытых передачах и в передачах с плохой (загрязняемой) смазкой усталостное изнашивание опережается абразивным износом активных поверхностей зубьев (рис. г).
В тяжелонагруженных и высокоскоростных передачах в зоне контакта зубьев возникает высокая температура, способствующая разрыву масляной пленки и образованию металлического контакта, в результате чего происходит заедание зубьев (рис. д), о резьбовых соединениях Резьбовым называют соединение... шаг резьбы, как и шаг зубьев зубчатых колес, будем обозначать строчной буквой... , упорная, прямоугольная) служат для передачи движения и применяются в передачах винт - гайка, которые будут...
Зубчатые передачи (3)
Реферат >>... зубчатых передачах 1.1 Общие сведения В зубчатой передаче движение передается с помощью зацеп ления пары зубчатых колес (рис. 1, а - в). Меньшее зубчатое ... масел. 2 ЦИЛИНДРИЧЕСКИЕ КОСОЗУБЫЕ ПЕРЕДАЧИ 1.1 Общие сведения Цилиндрические колеса, у которых...
Детали машин. Конспект лекций. Основные требования к конструкции деталей машин
Конспект >> Промышленность, производствоНатягом (прессовые соединения) Общие сведения Соединение двух деталей... . Поэтому ниже излагаются краткие сведения о контактных напряжениях и... потери, свойственные как зубчатой передаче , так и передаче винт-гайка. Общий К. П. Д. червячной передачи η , (5.25) ...
Валы и оси. Общие сведения
Научная статья >> Промышленность, производствоИ оси. Общие сведения Вал - деталь машин, предназначенная для передачи крутящего момента вдоль... вращающиеся вместе с ними детали (зубчатые колеса, шкивы, звездочки и др... валов может нарушить нормальную работу зубчатых колес и подшипников, следовательно, ...